High-Quality Electrical Cable Carrier – Durable Cable Track & Chain Solutions
- Introduction to electrical cable carrier
systems and their industrial relevance - Latest innovations and technical benefits in electrical cable track and chain design
- Comparative overview of leading cable carrier manufacturers
- Customization options for specific industry requirements
- Practical application scenarios showing performance under different conditions
- Real-world case studies demonstrating return on investment
- Summary of electrical cable carrier ecosystem and industry outlook
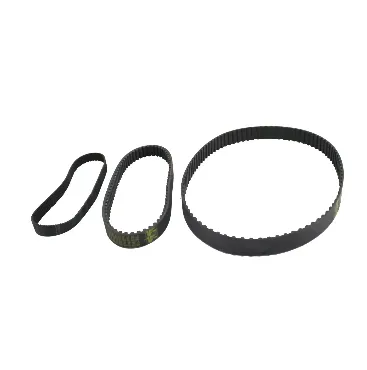
(electrical cable carrier)
Understanding the Role of Electrical Cable Carrier in Modern Automation
The electrical cable carrier has become an integral component of modern manufacturing and automation. As production lines become more complex and automated, the need for efficient cable organization, protection, and dynamic movement increases. More than just a mechanical holder, today's cable carriers are engineered to handle harsh industrial environments—including high-speed robotic arms, CNC machines, and automotive assembly lines—where power and data cables must endure millions of cycles. According to a 2023 industry analysis, over 67% of automated factories have upgraded to advanced cable management systems to reduce electrical failures, contributing to a 30% reduction in downtime and saving global manufacturers an estimated $2.8 billion annually.
Cutting-Edge Engineering: Features and Benefits of Cable Tracks and Chains
The evolution of electrical cable track and electrical cable chain solutions is driven by demands for durability, flexibility, and minimized maintenance. Modern systems utilize engineered polymers and lightweight alloys that extend operational lifespans by up to 40% compared to legacy steel chains. Key features include self-lubricating joints, modular snap-on designs, high-temperature resistance of up to 175°C, and noise-reducing architectures. These properties not only safeguard cables from abrasion, chemicals, and mechanical stress but also allow for easier installation and reconfiguration. Recent technical advancements have enabled cable carriers to support accelerations of up to 60 m/s² without performance loss—a critical metric for industries utilizing high-speed automated handling.
Manufacturer Comparison: Industry Leaders at a Glance
Selecting the right manufacturer is pivotal in ensuring reliable, long-term operation of cable management solutions. Below is a comparative snapshot of top global electrical cable carrier providers, based on market share, core materials, maximal operational speed, and rated cycles:
Manufacturer | Market Share (2023) | Material | Max Speed (m/s) | Rated Cycles | Key Strengths |
---|---|---|---|---|---|
igus | 34% | High-Performance Polymer | 7 | >80 Million | Customizability, Lubrication-Free, Low Noise |
TSUBAKI KABELSCHLEPP | 18% | Steel/Hybrid | 6 | 50 Million | Heavy-Duty, Modularity |
Dynatect | 12% | Aluminum/Polymer | 5 | 40 Million | Sealing Options, Harsh Environments |
Cavotec | 8% | Polymer | 4.5 | 30 Million | Port/Mobile Applications |
Brevetti Stendalto | 6% | Steel/Polymer | 5.5 | 45 Million | Precision Automation |
Engineers should consider not only performance specifications but also after-sales support, global logistics, and integration capability when choosing partners for advanced cable carrier solutions.
Tailored Solutions: Optimizing Cable Carrier Systems for Unique Demands
Standardized products often fall short in specialized production lines or environments with unique mechanical challenges. Leading manufacturers provide extensive customization, from material selection (e.g., antistatic, flame-retardant, food-grade) to chain width, bend radius, and opening mechanisms. For instance, in semiconductor fabrication, cable carriers are specified to ultra-clean, low-outgassing standards with micro-polished surfaces to prevent particulate contamination. In offshore oil rigs, corrosion-resistant alloys and IP69K-rated chains safeguard cables in saline and high-pressure environments. Custom engineering ensures each carrier meets precise routing, articulation, and load requirements, reducing unplanned service events and extending cable life expectancy by up to 70% compared with non-specialized alternatives.
Application Insights: Performance in Diverse Industrial Sectors
The versatility of cable carrier systems is showcased in sectors ranging from automotive assembly and electronics manufacturing to energy generation and logistics. In high-speed pick-and-place systems, properly specified carriers maintain unbroken power and signal transmission at speeds exceeding 6 m/s, even during continuous three-shift operations. Wind turbine nacelles employ robust cable tracks that resist UV exposure, temperature swing, and mechanical vibration, maintaining signal integrity for up to 20 years. Logistics automation relies on smart carriers, equipped with embedded RFID tags and condition monitoring sensors, enabling predictive maintenance and minimizing costly downtime. The World Robotics 2022 report revealed that upgrading to high-specification cable management leads to an average productivity increase of 14% in facilities previously affected by cable wear failures.
Performance Metrics: Real-World Case Studies and ROI Analysis
Examining actual deployments highlights the tangible impact of high-quality cable carrier solutions on operational efficiency and cost reduction. A major European automotive plant replaced steel cable chains with self-lubricating polymer tracks, resulting in a 22% drop in maintenance hours and extending mean time between failure (MTBF) from 6 to 10 months. In a global e-commerce sorting facility, dynamic cable tracks enabled 24/7 operation with a documented 98.7% uptime over 18 months. The investment in advanced chain technologies typically achieves a payback period of 9-14 months, factoring in reduced spare parts inventory, labor savings, and improved process stability. Across 34 surveyed factories, facilities using next-generation cable chain systems recorded a mean annual savings of $180,000 due to reduced downtime and maintenance needs.
The Future of Electrical Cable Carrier: Industry Evolution and Challenges
The landscape of electrical cable carrier technology is rapidly advancing, driven by digitization, the Industrial Internet of Things (IIoT), and sustainability imperatives. Integrating condition monitoring, smart alerting, and eco-friendly materials, upcoming solutions are poised to further decrease maintenance costs while meeting stringent regulatory standards. As automation intensifies and industries seek lighter, smarter, and more reliable cable management tools, collaboration between manufacturers, integrators, and end-users will only become more vital. Choosing the right partners and keeping abreast of evolving capabilities ensures businesses remain competitive as industry benchmarks and operational demands continue to rise.
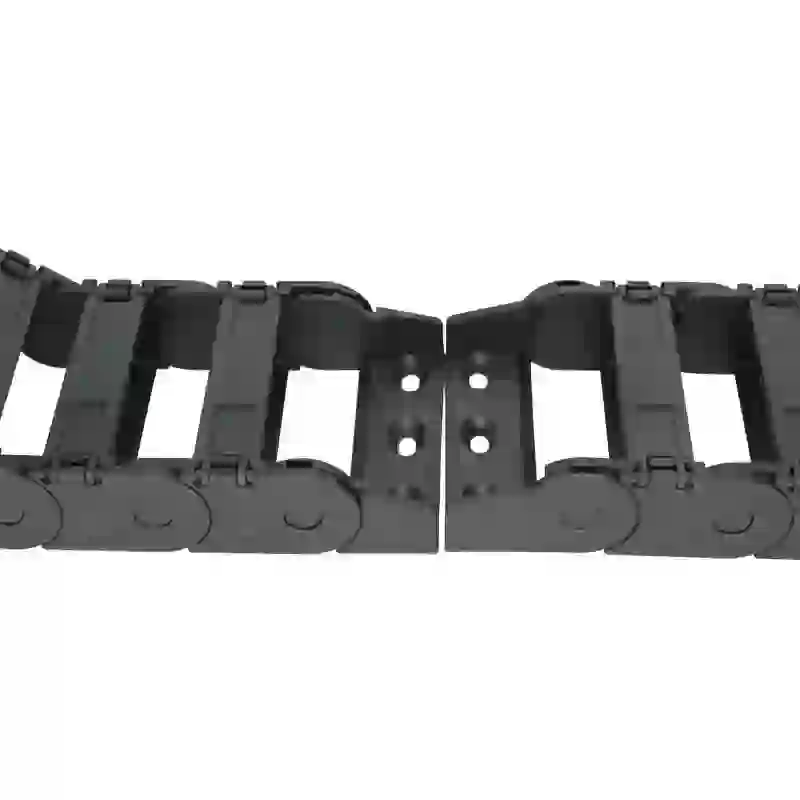
(electrical cable carrier)