Efficient Solutions for Managing CNC Cables with Durable Track Systems for Optimal Performance
Understanding CNC Cable Tracks The Backbone of Efficient CNC Machinery
In the realm of modern manufacturing, CNC (Computer Numerical Control) machinery stands as a hallmark of precision and efficiency. A critical component that enhances the performance and reliability of CNC systems is the cable track, also known as a drag chain or energy chain. This essential item facilitates the organized and efficient management of various cables and hoses associated with CNC machinery, ensuring seamless operation.
What is a CNC Cable Track?
A CNC cable track is a flexible conduit designed to guide and protect the cables and hoses that connect the machinery to power sources, control systems, and pneumatic systems. Think of it as a train track for cables, designed to ensure that these essential components are safely organized and do not get tangled or damaged during the operation of CNC machines.
Typically made from durable materials such as nylon, plastic, or steel, cable tracks come in various sizes and configurations to suit different applications. Their design often includes features to reduce friction and wear, ensuring that the cables can move freely without obstructing the machine’s operation.
Importance of CNC Cable Tracks
1. Organization and Safety One of the primary functions of a cable track is to keep cables organized. In a busy manufacturing environment, unkempt cables can pose safety hazards, leading to tripping hazards and damage to the components. Cable tracks help maintain neat cable routes, minimizing these risks.
2. Movement Flexibility CNC machines often undergo rapid movements, whether operating on a 3-axis or more sophisticated multi-axis system. Cable tracks are designed to allow for free movement in multiple directions while ensuring that the wires inside them are not pinched, twisted, or damaged. This flexibility is crucial for the performance and longevity of both the cables and the machinery.
cnc cable track
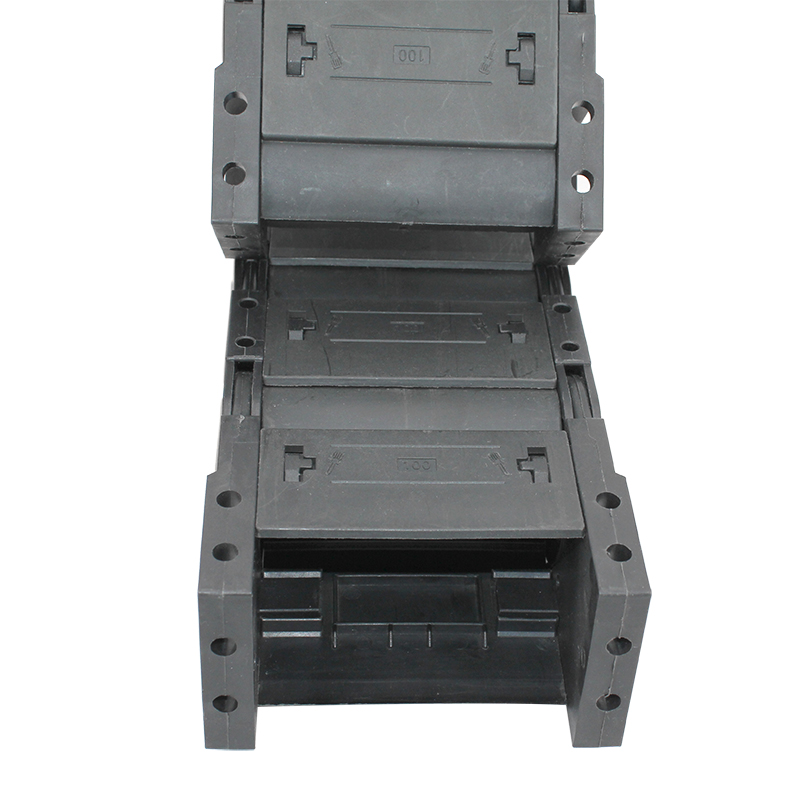
3. Protection Cables are vulnerable to wear and tear from the harsh environment of manufacturing facilities. Dust, debris, and mechanical stress can lead to insulation damage or electrical failures. CNC cable tracks provide a protective shield over these cables, safeguarding them from such potential harm, thereby reducing maintenance costs and downtime.
4. Efficiency Efficient cable management translates directly into improved machine performance. When cables are positioned correctly, machines can operate smoother and faster. This efficiency can significantly impact production output and overall operational costs, which are critical in competitive manufacturing sectors.
5. Customizability With a variety of sizes, shapes, and materials available, CNC cable tracks can be customized to fit the specific needs of any CNC setup. This adaptability makes them suitable for many applications, from simple milling machines to complex robotic systems.
Maintenance and Care
To ensure the longevity and efficiency of CNC cable tracks, regular maintenance is necessary. Operators should inspect the tracks for wear, ensure that they are clean, and check for any signs of cable damage. Keeping the tracks lubricated and free of debris will help maintain their flexibility and function.
Conclusion
CNC cable tracks are more than just a functional component of CNC machinery; they are essential to ensuring a safe, efficient, and organized manufacturing process. By protecting and guiding the cables that power these advanced machines, cable tracks help manufacturers optimize their operations, reduce costs, and maintain high productivity levels. As technology continues to evolve and increase in complexity, the importance of reliable and innovative cable management solutions will only continue to grow. In this fast-paced industry, investing in quality CNC cable tracks is a step towards achieving operational excellence.