Durable High Tensile Drag Chains for Enhanced Performance and Reliability in Industrial Applications
High Tensile Drag Chains Essential Components for Modern Machinery
In the realm of industrial automation and machinery, drag chains have emerged as vital components that ensure the seamless operation of equipment. Among these, high tensile drag chains are particularly noteworthy, providing solutions that address challenges associated with the demanding environments of various manufacturing and industrial settings.
Understanding Drag Chains
Drag chains, also known as energy chains or cable carriers, are systems designed to manage and protect cables, hoses, and other flexible media. Their primary function is to guide and support these items as they move with machinery, preventing tangling, abrasion, and mechanical wear. The design of drag chains allows them to carry various cables efficiently while maintaining a tidy and organized workspace.
The Need for High Tensile Strength
High tensile drag chains are specifically engineered to withstand significant loads and stresses. In today’s fast-paced industrial environment, machinery operates under extreme conditions, from high-speed movements to heavy loads. Standard drag chains may not endure such demands, leading to premature wear, equipment failure, and costly downtime. High tensile drag chains address this issue by utilizing robust materials and innovative engineering designs that enhance their strength and durability.
Material Composition and Design
The materials used in high tensile drag chains are crucial to their performance. Typically crafted from high-performance plastics or metal alloys, these drag chains offer excellent resistance to wear, impact, and environmental factors. The design often incorporates features such as reinforced links, which distribute stress evenly and enhance load-bearing capacity. Additionally, some high tensile drag chains include integrated wear strips or cushioning elements to further reduce friction and prolong lifespan.
Applications Across Industries
high tensile drag chain
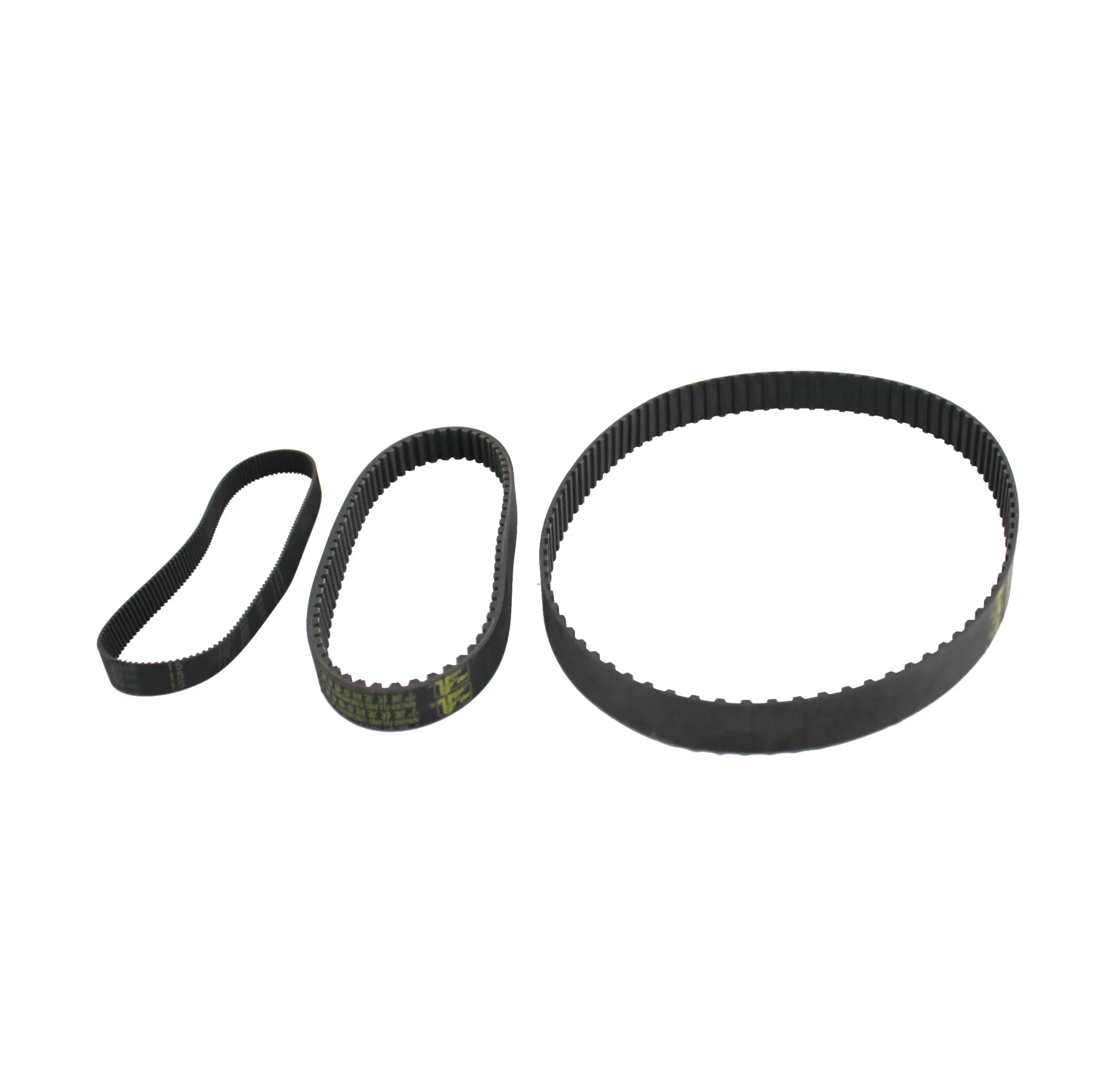
High tensile drag chains are utilized across various industries, including manufacturing, robotics, aerospace, and automotive
. In robotics, for example, these chains are essential for ensuring the reliable movement of cables in robotic arms, preventing interference that could disrupt operations. In manufacturing facilities, high tensile drag chains are deployed in conveyor systems and automated machinery, where immense loads and swift movements are commonplace.Moreover, they are invaluable in environments where exposure to chemicals or extreme temperatures is a concern. High tensile drag chains can be designed to resist corrosion and withstand temperature fluctuations, making them suitable for industries such as food processing and pharmaceuticals.
Advantages of High Tensile Drag Chains
1. Durability The primary advantage of high tensile drag chains is their longevity. Their ability to handle high loads without compromising structural integrity leads to reduced maintenance costs and increased operational efficiency.
2. Safety By keeping cables organized and protected, these drag chains minimize the risks associated with cable damage, which can lead to potential safety hazards in the workplace.
3. Flexibility High tensile drag chains are designed to accommodate a range of applications and configurations, making them versatile solutions for diverse machinery.
4. Efficiency By providing a reliable conduit for cables and hoses, high tensile drag chains enhance the overall performance of machinery, allowing for smoother operations and increased productivity.
Conclusion
In conclusion, high tensile drag chains are indispensable components in modern machinery, enhancing efficiency and safety in industrial environments. Their robust design and materials provide the strength required to meet the challenges of today’s demanding applications. As industries continue to evolve and automate, the role of high tensile drag chains will undoubtedly expand, further solidifying their position as essential elements in the machinery of the future. Embracing these advanced solutions will not only improve operational performance but also contribute to a more organized and safer industrial workspace.