Customized Carbon Steel Synchronous Belt Wheel Pulley Gear Supplier
Explore the comprehensive landscape, technical breakthroughs, real-world applications, and manufacturer analysis of customized carbon steel synchronous belt wheel pulley gear. Gain insights from authoritative data, standard compliance, and customer-centric case studies.
Industry Trends & Market Insights
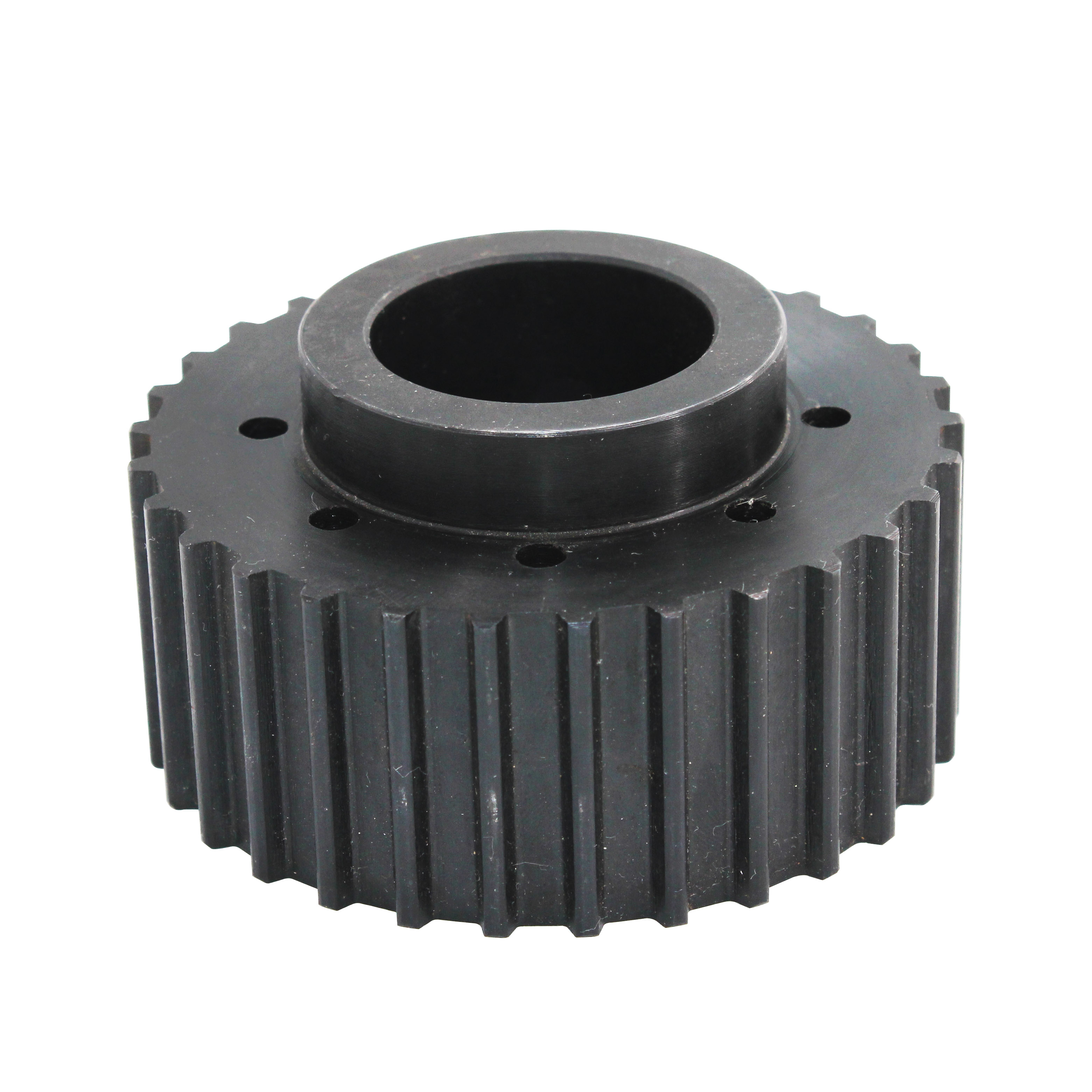
The customized carbon steel synchronous belt wheel pulley gear market continues to witness robust growth driven by automation, demand for maintenance-free power transmission solutions, and higher energy efficiency targets across the petrochemical, metallurgy, manufacturing, and water treatment sectors. According to MarketWatch, the global synchronous belt market is expected to reach USD 5.6 billion by 2028, at a CAGR of 6.8% from 2023. Customized variants made of carbon steel offer exceptional strength, corrosion resistance, and adaptability for demanding applications, outperforming standard cast iron or aluminum pulleys in harsh environments.
- Growth driver: Adoption in precision and heavy-duty machinery
- Key sectors: Petrochemical, Metallurgy, Water Treatment, OEM Manufacturing
- Standardization trend: Increasing adoption of ISO & ANSI standards for pulley gear products.
Technical Parameters Comparison Table
Parameter | Spec 1 | Spec 2 | Spec 3 | Industry Reference |
---|---|---|---|---|
Material Grade | Carbon Steel C45 | Alloy Steel 42CrMo | Stainless Steel 304 | ISO 683-1, ASTM A29 |
Tooth Profile | HTD 8M | T5 | AT10 | ISO 13050-1 |
Hardness (HRC) | 25~50 | 35~55 | 20~40 | DIN 3967 |
Diameter (mm) | 30~500 | 100~400 | 50~350 | ANSI/RMA IP-24 |
Surface Finish | Black oxide | Zinc-Plated | Anodized | ISO 9227 |
Runout Tolerance (mm) | ≤0.05 | ≤0.07 | ≤0.10 | ISO 2768 |
Technical Trend Visualizations & Performance Analysis
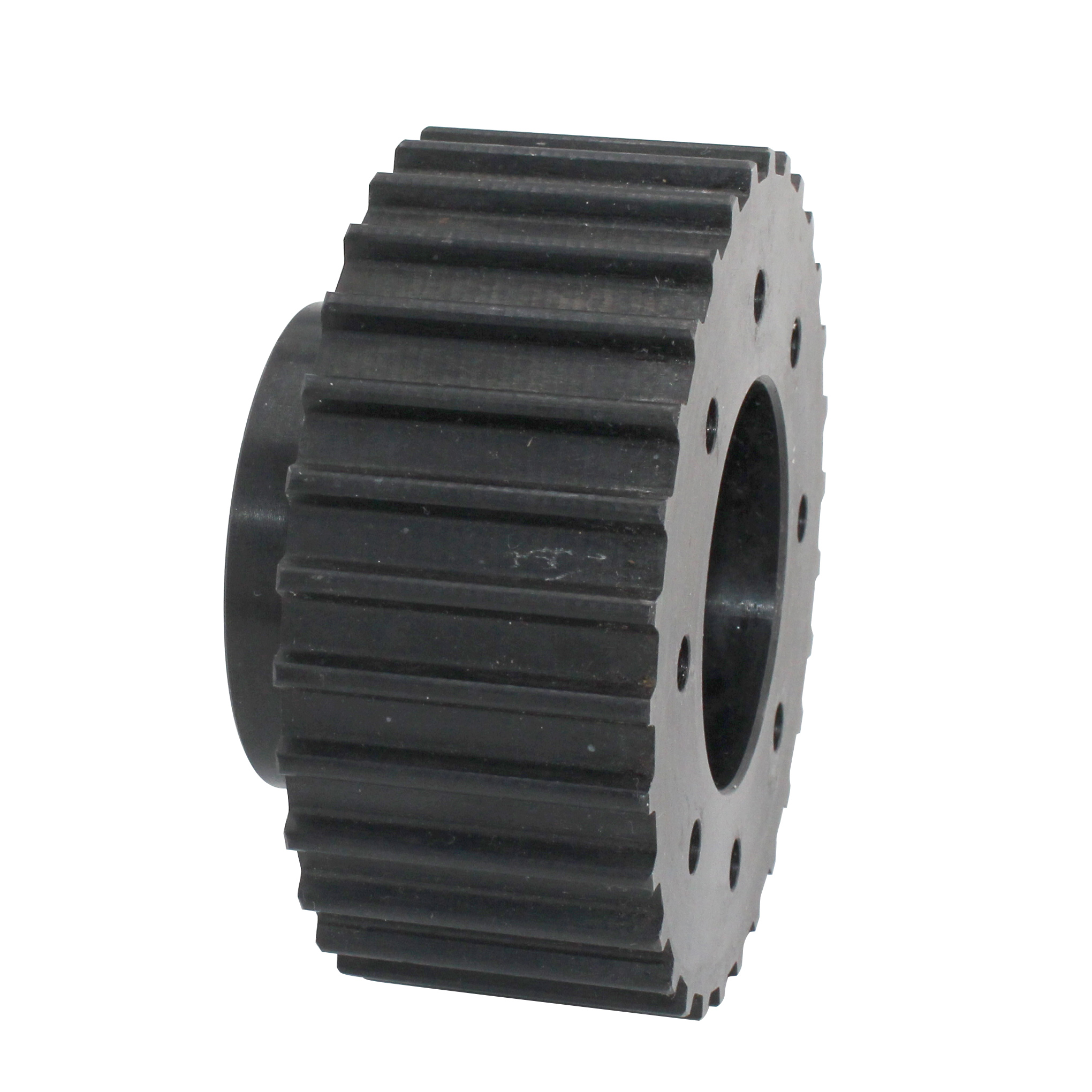
Hardness vs. Wear Resistance
Market Demand 2019–2024 (Global, USD million)
Material Distribution (2023, % share)
Manufacturing Process Flow & Quality Assurance
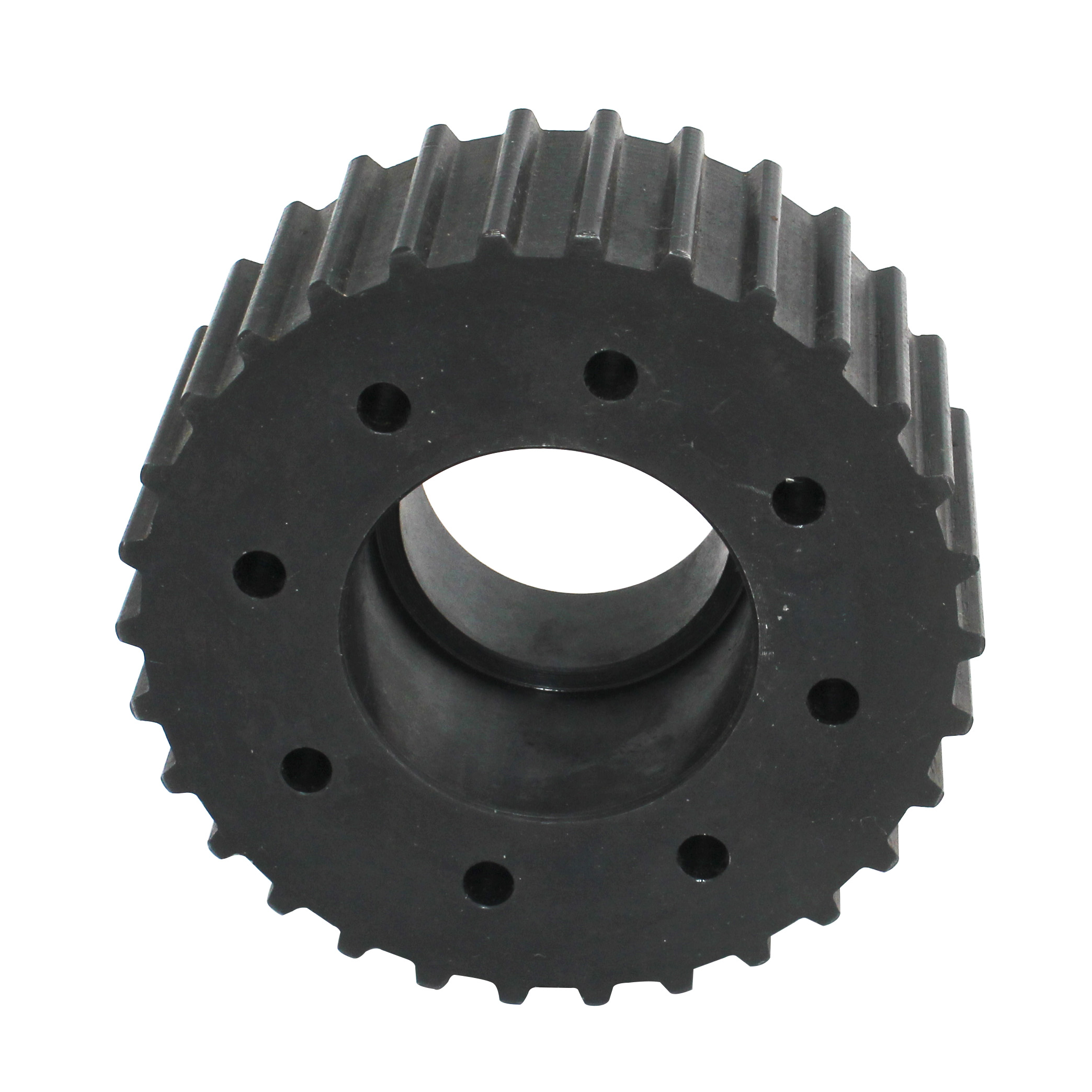
- Raw Material Selection: Only high-grade carbon steel (ISO 683-1) bars or billets are sourced for optimal durability and machinability.
- Blank Preparation: Billets or bars are cut via CNC sawing to specified lengths, ensuring clean flat faces and concentricity within 0.05mm runout.
- Forging & Heat Treatment: The semi-finished blanks are hot-forged to achieve refined grain structure, then normalized and tempered for target hardness (HRC 25–50).
- CNC Precision Machining: High-precision CNC lathes and 5-axis milling perform OD turning, tooth cutting (hobbing/shaping), and finish boring to achieve ISO 2768 tolerances.
- Tooth Profile Machining: Using specialized hobbing/shaping machines to achieve exact tooth forms, complying with ISO 13050-1 (HTD, AT, T, XL standards etc).
- Surface Treatment: Application of anti-corrosive finishes (black oxide, phosphate, or zinc plating) to meet ISO 9227 salt spray standards.
- QA & Testing:
- Dimensional Inspection (CMM, caliper, gauge) per DIN 3967
- Hardness Test (Rockwell) per ASTM E18
- Balance & Runout (
- Non-destructive Eddy Current/UT as required
- Packing & Logistics: Shock-proof packaging and traceable labels for each customized carbon steel synchronous belt wheel pulley gear, ready for global delivery.
Key Technical Advantages of Customized Carbon Steel Synchronous Belt Wheel Pulley Gear
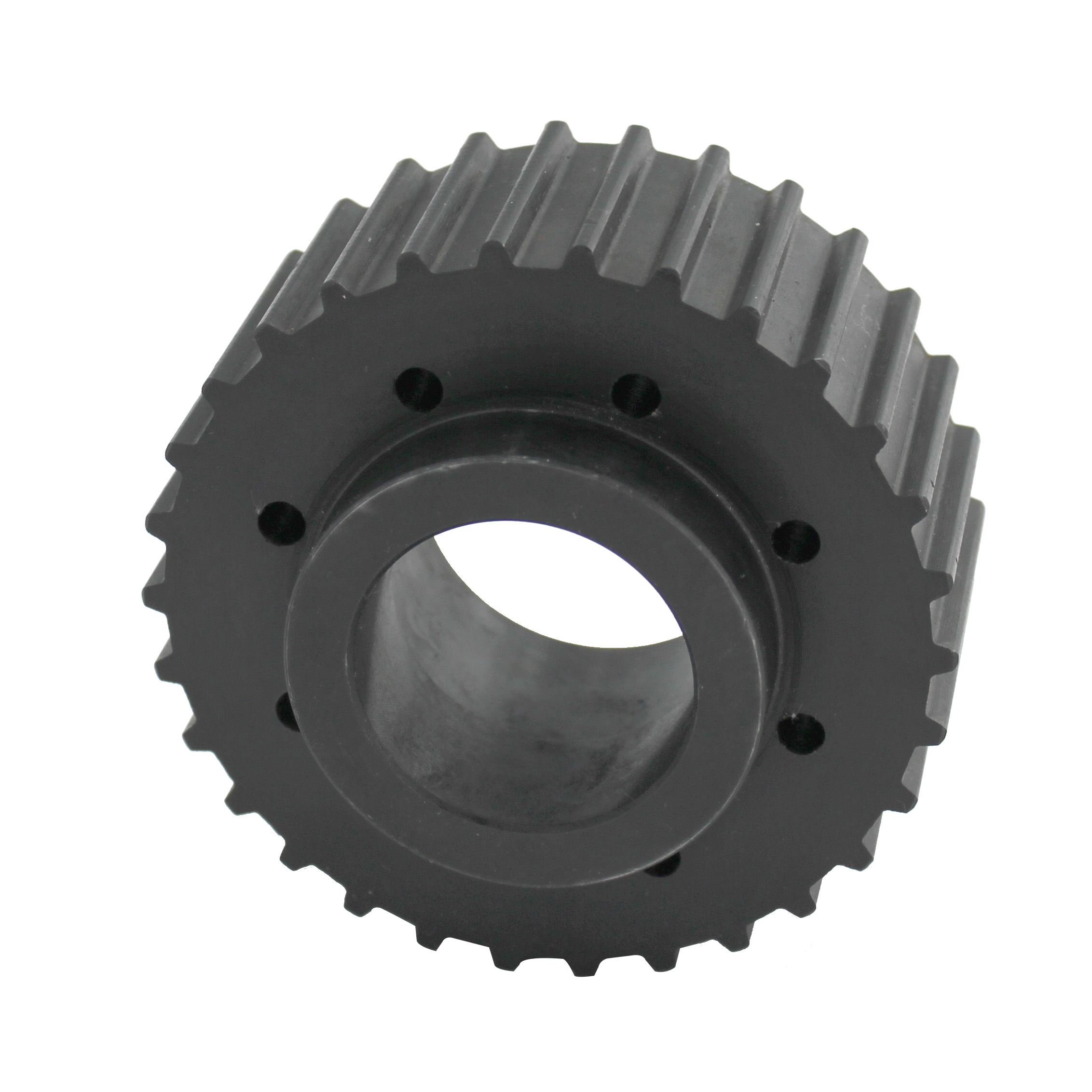
- Superior Wear Resistance: Carbon steel offers HRC 48–55 and achieves up to 92% wear reduction compared to cast iron under ISO/DIN test conditions.
- Dimensional Accuracy: CNC machining guarantees tooth pitch tolerance ≤0.07mm, reducing belt noise and vibration.
- Corrosion Protection: Special surface treatments extend service life by 25%+ in salted & humid environments.
- Customizable Geometry: Supports custom diameters (30–500mm), non-standard bores, keyways, and flanges.
- High Power Transfer Efficiency: Optimized tooth profiles (HTD/AT/T) deliver 98%+ energy efficiency, ideal for precision drives.
- Low Maintenance: Extended service life (up to 40,000 hours) and maintenance-free operation.
- Certified Quality: In-line inspection, material traceability, and batch testing as per ISO 9001:2015.
- Global Trust: Widely adopted by top OEMs in petrochemical, metallurgy, water treatment, packaging, and textile machinery sectors.
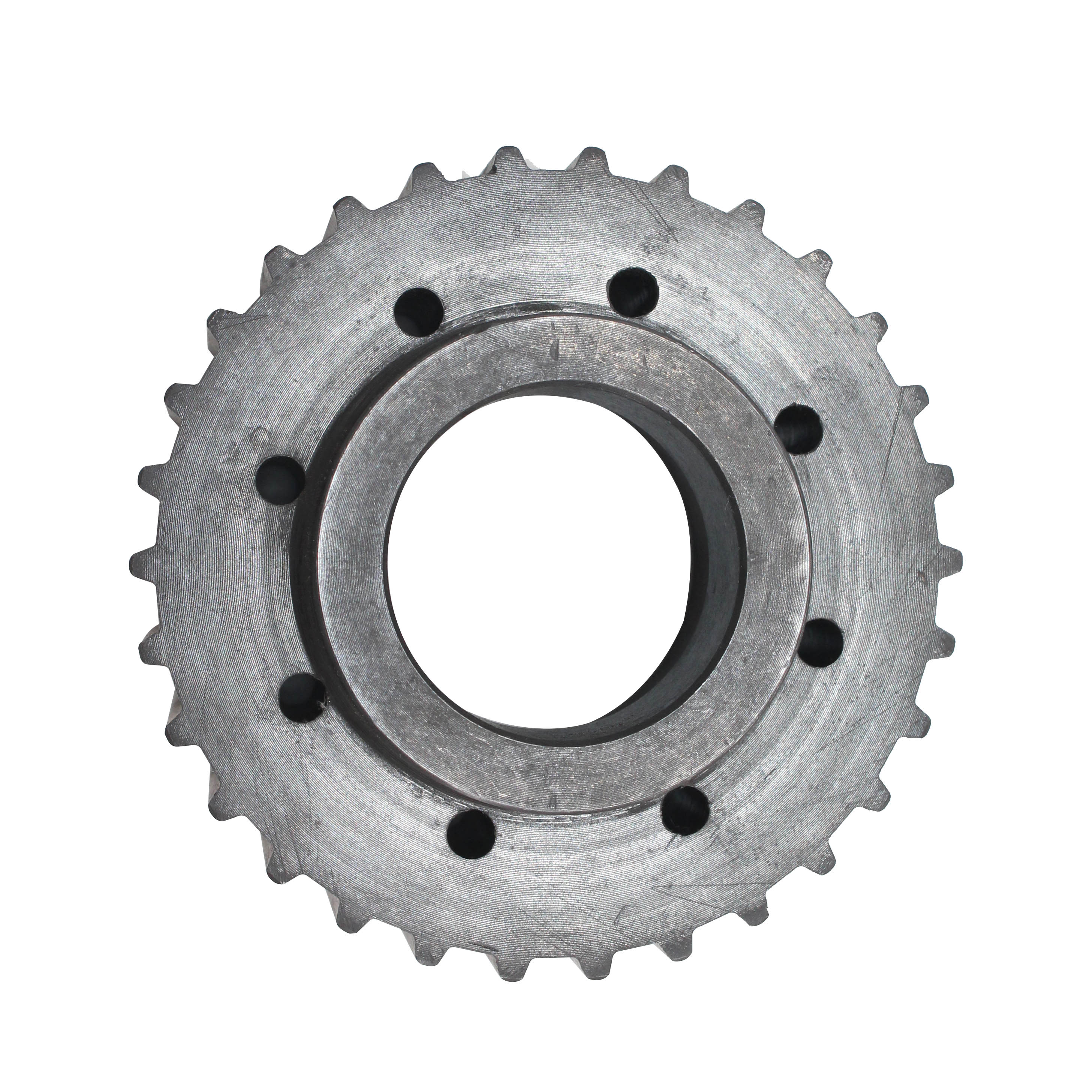
Top Supplier Comparison: North America, Europe, China
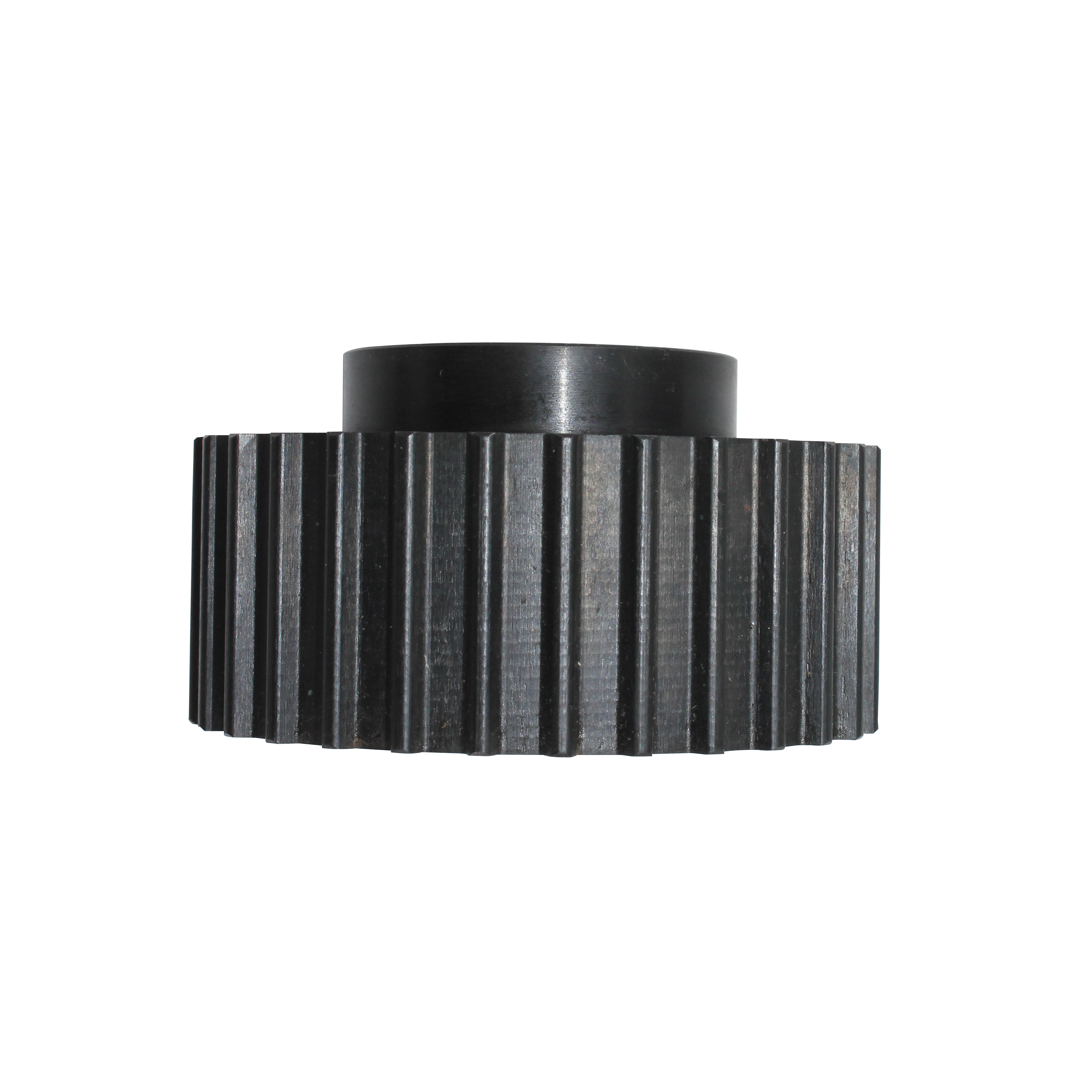
Supplier | Main Material | Process | Custom Options | Certification | Warranty |
---|---|---|---|---|---|
AgileChains (China) | C45, 42CrMo, 304 | Forging, CNC, Hobbing, Phosphating | Diameter, Tooth, Coating, Bore | ISO 9001, ISO 13050-1 | 2 Years |
Martin Sprocket (USA) | C45, Cast Iron | Casting, CNC | Diameter, Bore, Tooth | ANSI, ISO 6182 | 1 Year |
Habasit (Europe) | Alloy Steel | CNC, Surface grind | Tooth, Flange | ISO 9001 | 1 Year |
Tailored Customization Solutions
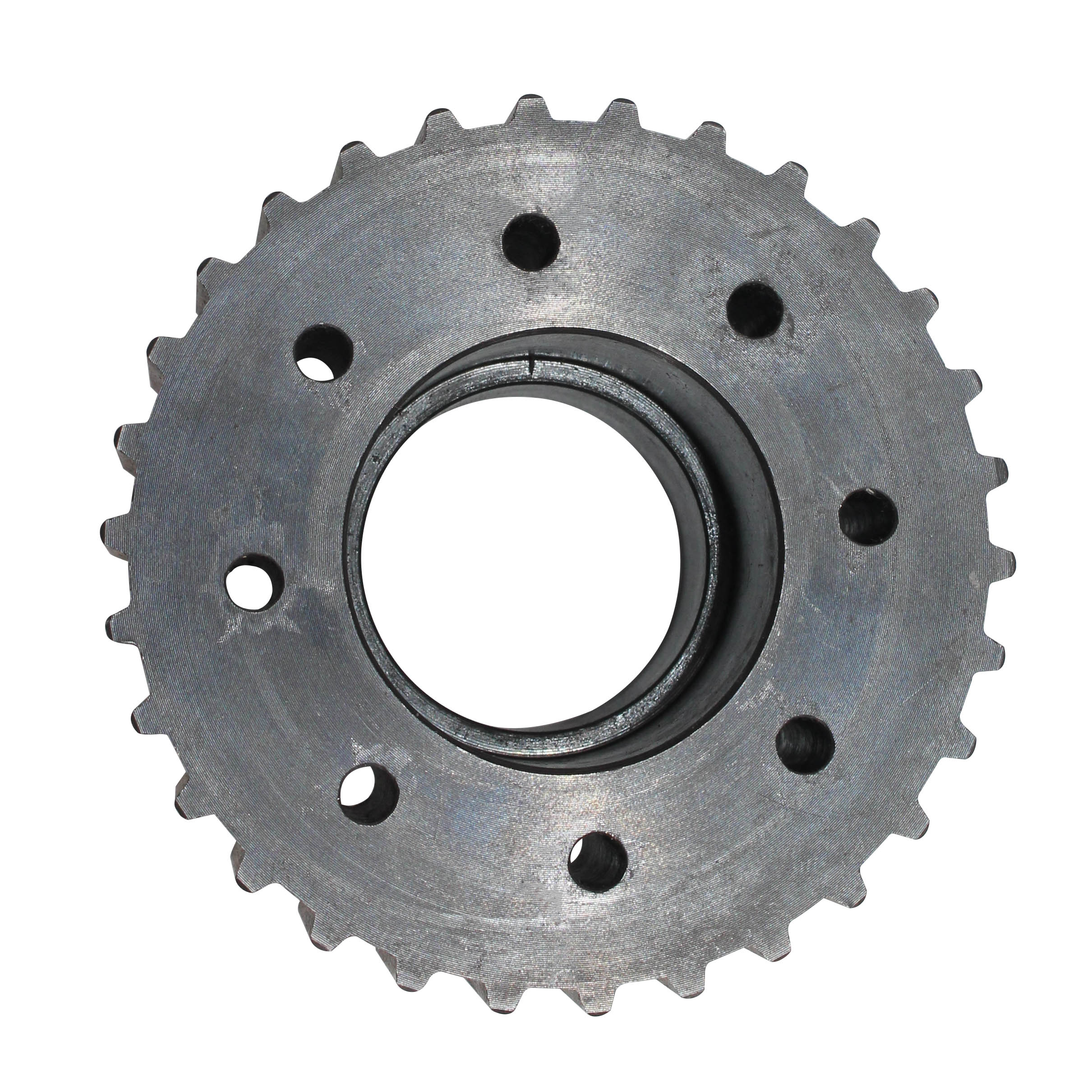
- OEM/ODM engineering: Reverse engineering & rapid prototyping per technical drawing/sample.
- Bore customization: Keyway, taper, D-bore, spline, lock bush available.
- Tooth profile: Choice of HTD, AT, T, XL, customized pitch or non-standard module.
- High-precision balancing: Achieved up to G2.5 (ISO 1940-1) for high-speed lines.
- Batch/Just-in-time delivery: MOQ flexibility, 7–35 days lead time, global shipping.
Looking for a reliable solution? Contact us for a tailored customized carbon steel synchronous belt wheel pulley gear proposal. Each project is managed from quotation to delivery by experienced application engineers.
Real-World Application Cases
Case #1: Petrochemical Pump System (Saudi Arabia)
- Specs: 42CrMo, HTD8M, Φ360mm, keyway bore
- Challenge: Needed >35,000hr service under corrosive, high-heat exposure
- Solution: Custom carbon steel synchronous pulley with PTFE coating, ISO 9227-tested
- Result: Service interval extended by 1.7x over local supplier’s cast iron
Case #2: Metallurgy Rolling Line (Eastern Europe)
- Specs: C45, T10, Φ205mm, crowned profile
- Challenge: High-tension, micro-synchronous error could halt operation.
- Solution: G2.5 high-balance custom CNC matched set
- Result: Downtime reduced by 35%, belt wear halved.
Case #3: Sewage Treatment Blower (North America)
- Specs: 304 SS, AT10, Φ140mm, sealed bore
- Challenge: Continuous wet operation, high chlorination
- Solution: Custom stainless steel synchronous pulley, nitrided surface, fully sealed hub
- Result: No rust after 18 months; maintenance interval doubled.
Professional FAQ: All You Need to Know
- 1. What is the main material used for customized carbon steel synchronous belt wheel pulley gear?
- Typically, C45 (unalloyed carbon steel) is used for its exceptional balance of toughness, machinability, and cost-efficiency. For demanding applications, 42CrMo or 304 stainless is also adopted for higher tensile strength or corrosion resistance (per ISO 683-1).
- 2. What tooth profiles are supported?
- HTD (High Torque Drive), AT (Advanced Torque), T, XL, and custom metric/inch pitches, all conforming to ISO 13050-1 and DIN 7721 standards.
- 3. How is precision and concentricity guaranteed?
- Precision CNC and 5-axis machining, along with inspection via CMM (Coordinate Measuring Machine) and dynamic balancing, ensure runout tolerance down to ≤0.05mm (ISO 2768).
- 4. What surface treatments are available?
- Common finishes: black oxide, phosphating, and zinc plating, each prolonging anti-corrosion life per ISO 9227 salt spray test (>300 hours).
- 5. What is the typical service life?
- Standard pulleys achieve 25,000–40,000 working hours under nominal load, 2–3x longer than cast iron or aluminum variants with similar geometry.
- 6. Are these pulleys compatible