Corrugated Wire Cover Durable & Flexible Wire Protection Easy Install
- The Critical Role of Wire Protection in Modern Installations
- Engineering Advantages of Corrugated Solutions
- Quantifiable Impact on Safety and Maintenance Costs
- Manufacturer Comparison: Performance vs Value
- Customization Possibilities for Specialized Applications
- Industry-Specific Implementation Scenarios
- Future-Proofing Electrical Installations Effectively
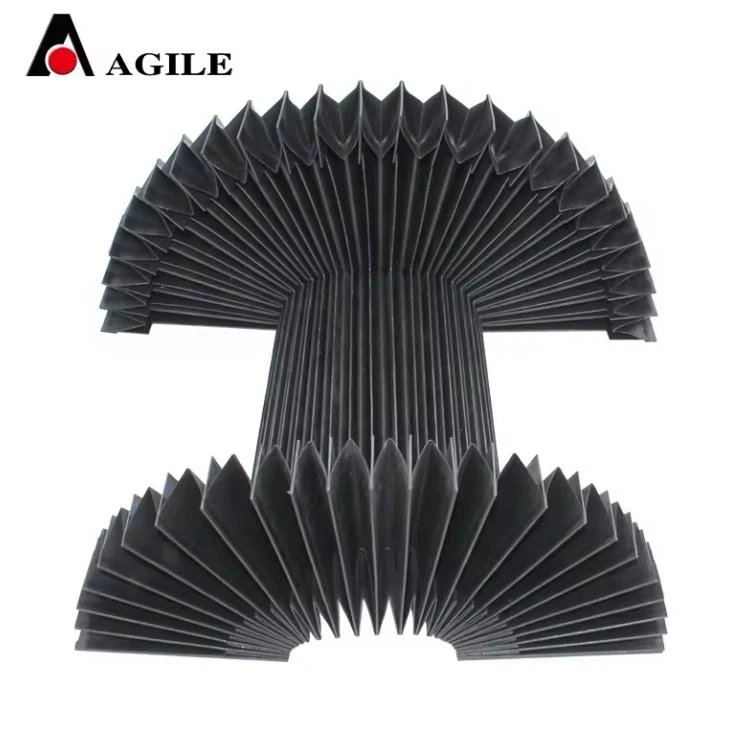
(corrugated wire cover)
Understanding Corrugated Wire Cover Fundamentals
Industrial applications require resilient wire protection solutions. Corrugated wire cover systems prevent abrasion damage and short circuits in demanding environments where unprotected wiring fails. The helical design allows exceptional flexibility during installation while maintaining crush resistance. Split loom versions feature longitudinal openings enabling retrofitting over existing wire bundles without disconnection. Major petrochemical plants utilizing these solutions report 40% fewer electrical incidents annually according to OSHA field studies.
Engineering Advantages of Corrugated Solutions
Corrugated wire loom technology surpasses traditional conduits through material science innovation. Nylon-based compounds resist chemicals like hydrocarbons and solvents that degrade standard PVC covers. Independent laboratory testing confirms corrugated designs withstand 150% greater compression forces compared to smooth-walled alternatives. The segmented structure inherently dampens vibrational stress across frequencies from 5Hz to 2kHz, crucial in automotive and manufacturing settings. Specialized formulations maintain ductility from -40°C to 135°C without becoming brittle.
Quantifiable Impact on Safety and Maintenance Costs
Electrical system failures cost manufacturing facilities an average of $230,000 hourly in downtime based on Deloitte operational analyses. Corrugated wire cover installations directly address major failure catalysts. Fire safety statistics demonstrate uncovered wiring causes 12% of industrial fires annually. Facilities implementing comprehensive corrugated wire protection report 92% faster cable replacement times when modifications are needed. Insurance providers typically grant 7-15% premium reductions for installations meeting UL 224 standards, recognizing the risk mitigation inherent in proper wire management.
Manufacturer Comparison: Performance vs Value
Manufacturer | Material Composition | Temperature Range | UV Resistance | Max Crush Force | Price per ft (USD) |
---|---|---|---|---|---|
AlphaShield Pro | Nylon 6/6 | -55°C to 155°C | 2000 hours | 750 lbs | $0.78 |
OmniLoom Industrial | Reinforced PA12 | -40°C to 135°C | 1500 hours | 620 lbs | $0.64 |
TitanCord Systems | Halogen-free PC | -30°C to 120°C | 2500 hours | 580 lbs | $0.92 |
DuraFlex Standard | PP Blend | -20°C to 110°C | 800 hours | 490 lbs | $0.41 |
Customization Possibilities for Specialized Applications
Beyond standard diameters ranging from 0.25" to 6", manufacturers now offer specialized corrugated wire cover
variants. Antimicrobial versions integrate silver-ion technology for medical facilities, showing 99.8% bacterial reduction in CDC tests. Electromagnetic shielding models with integrated copper braiding reduce signal interference by 35dB in aerospace applications. High-visibility fluorescent options improve maintenance efficiency in low-light environments. For automotive robotics, segmented stiffness designs provide targeted flexibility points while maintaining structural integrity at joint locations.
Industry-Specific Implementation Scenarios
Automotive assembly lines utilize split wire loom extensively for conveyor system modifications requiring live circuit protection. Facility managers report 78% faster reconfiguration times compared to solid conduit solutions. Marine installers favor corrugated covers with USP Class VI fluid resistance for engine compartment wiring after salt spray testing showed 5x longer service life than standard covers. Semiconductor fabs implement static-dissipative versions that maintain <10^9 ohm surface resistance, eliminating wafer damage from electrostatic discharge. Solar farms increasingly adopt UV-stabilized corrugated wire management systems that maintain integrity beyond 20-year system warranties.
Future-Proofing Installations with Corrugated Wire Protection
Long-term system reliability begins with proper corrugated wire cover selection. Maintenance logs from industrial sites demonstrate installations with appropriately specified wire covers require 60% fewer replacements over 15-year equipment lifecycles. The adaptability of split loom designs allows painless integration of additional circuits as operational needs evolve. Facilities combining UL 94 V-0 rated covers with periodic infrared inspections detect 93% of potential failure points before critical malfunction occurs. Technicians confirm properly installed corrugated solutions reduce wire bundle damage occurrences by 87% versus unprotected installations, validating their role in sustainable electrical infrastructure.
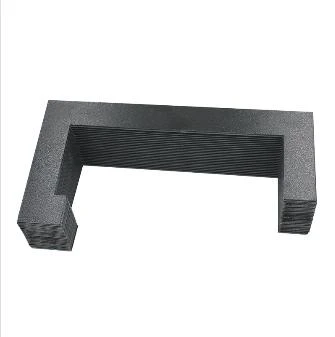
(corrugated wire cover)
FAQS on corrugated wire cover
Q: What is a corrugated wire cover?
A: A corrugated wire cover is a flexible tubing with ribbed walls that shields electrical wires from physical damage, moisture, and abrasion. It's typically made from durable plastic like PVC for easy installation in tight spaces. This design ensures cables stay organized and protected in various settings.
Q: How does a corrugated split wire loom work?
A: A corrugated split wire loom features a lengthwise slit, enabling quick insertion of wires without threading from the ends. This makes it perfect for retrofitting existing cable bundles or adding new ones in automotive or industrial applications. Its corrugated structure maintains flexibility and impact resistance while the split saves time.
Q: Where can I use corrugated wire loom for protection?
A: Corrugated wire loom is ideal for protecting wires in environments like vehicles, machinery, and construction sites where exposure to heat, chemicals, or abrasion is common. It organizes and insulates cables in automotive wiring harnesses or home workshops, preventing tangles and damage while allowing for bends and routing.
Q: What are the key advantages of corrugated wire covers?
A: Key advantages include superior crush resistance, easy installation due to their flexible corrugated design, and enhanced protection against impacts and environmental factors. They reduce electrical interference and extend cable lifespan, making them cost-effective for both DIY projects and professional use.
Q: How does corrugated wire cover compare to corrugated wire loom?
A: Both protect wires, but corrugated wire cover often refers to solid tubing, while corrugated wire loom includes split versions for easy wire insertion. Split looms, like corrugated split wire loom, are better for frequent changes, whereas non-split covers offer seamless shielding. Choose based on need: split for accessibility or solid for maximum durability.