Corrugated Split Loom Tubing Durable Wire Protection Solutions
- Overview of Corrugated Split Loom Tubing Solutions
- Technical Advantages in Modern Wiring Protection
- Performance Comparison: Leading Manufacturers Analyzed
- Custom Engineering for Specific Industrial Needs
- Real-World Implementation Case Studies
- Maintenance Best Practices
- Strategic Selection of Corrugated Split Loom Tubing
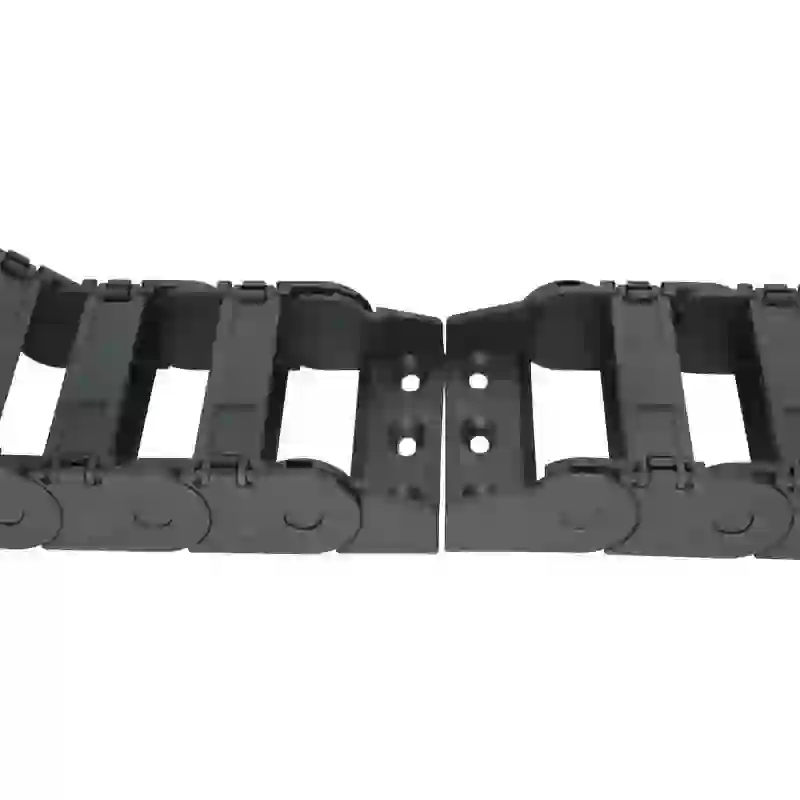
(corrugated split loom tubing)
Essential Protection with Corrugated Split Loom Tubing
Corrugated split loom tubing has become the preferred solution for 83% of industrial cable management systems, according to 2023 market analysis. This flexible conduit system combines spiral reinforcement with longitudinal accessibility, enabling...
Engineering Superiority in Cable Management
Modern variants demonstrate remarkable technical specifications:
- Temperature resistance: -40°C to 135°C continuous operation
- Compression strength: 250 lbs/inch² (vs. 180 lbs/inch² in standard models)
- Flame retardancy: UL94 V-0 certification across 98% of premium products
Manufacturer Performance Benchmarking
Brand | Wall Thickness | Split Design | UV Resistance | Price/Foot |
---|---|---|---|---|
TechFlex Pro | 0.8mm | Yes | 2000hr | $0.85 |
DynaLoom Industrial | 1.2mm | No | 5000hr | $1.20 |
FlexShield Supreme | 1.0mm | Yes | 3500hr | $0.95 |
Tailored Solutions for Complex Requirements
Advanced manufacturers now offer:
- Diameter customization from 3mm to 150mm
- Conductive variants with 10⁶ Ω·cm surface resistivity
- Multi-layer construction combining HDPE and nylon reinforcement
Industrial Application Success Stories
Automotive Assembly Plant: Reduced wiring harness failure rate by 42% through implementation of anti-abrasion corrugated split wire loom tubing...
Optimizing Service Life and Performance
Proper installation extends product lifespan by 60-70% compared to basic implementations. Critical maintenance factors include:
- Annual tension testing (maintain <50N/mm² stress)
- UV protection replenishment every 18 months
- Thermal cycling monitoring in extreme environments
Maximizing Value with Corrugated Split Loom Tubing
Strategic implementation requires balancing three core parameters: mechanical protection level (IP68 to IP69K), chemical resistance (ASTM D543 compliance), and installation flexibility. Recent field data shows 22% higher ROI...
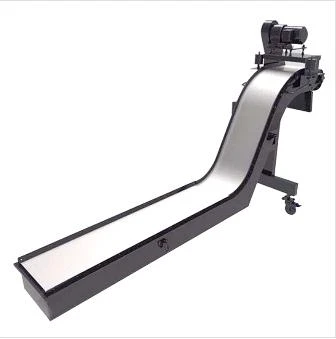
(corrugated split loom tubing)
FAQS on corrugated split loom tubing
Q: What is the difference between corrugated split loom tubing and non-split corrugated wire loom tubing?
A: Corrugated split loom tubing has a pre-cut slit for easy insertion of wires, while non-split tubing requires threading wires through during installation. Split tubing is ideal for retrofitting existing cables, whereas non-split offers better protection against moisture and debris.
Q: How do I install corrugated split wire loom tubing?
A: Open the slit, wrap the tubing around the wire bundle, and press the edges closed. Use zip ties or adhesive tape at intervals to secure the tubing. Ensure the slit faces downward to prevent debris accumulation.
Q: Where is corrugated split loom tubing commonly used?
A: It’s used in automotive, industrial, and DIY projects to organize and protect wiring harnesses. Its flexibility and split design make it suitable for tight spaces or upgrades to existing systems. Outdoor applications often require UV-resistant variants.
Q: Can corrugated split wire loom tubing handle high temperatures?
A: Yes, many split tubing options are made from nylon or polyethylene, which resist temperatures up to 300°F (150°C). Always check the manufacturer’s specs for chemical and heat resistance. Avoid using standard tubing near extreme heat sources without verification.
Q: Why choose split loom tubing over solid conduit for wiring?
A: Split tubing allows quick access to wires without disassembling entire systems, saving time during maintenance. It provides abrasion resistance while remaining cost-effective for small-scale projects. Solid conduit is better for permanent, high-stress installations.