Durable Corrugated Metal Conduit for Industrial Wiring & Protection
- Introduction to Conduit Infrastructure
- Technical Performance Capabilities
- Industry Supplier Comparison
- Customization Specifications
- Industrial Deployment Scenarios
- Installation Methodologies
- Industry Development Trajectory
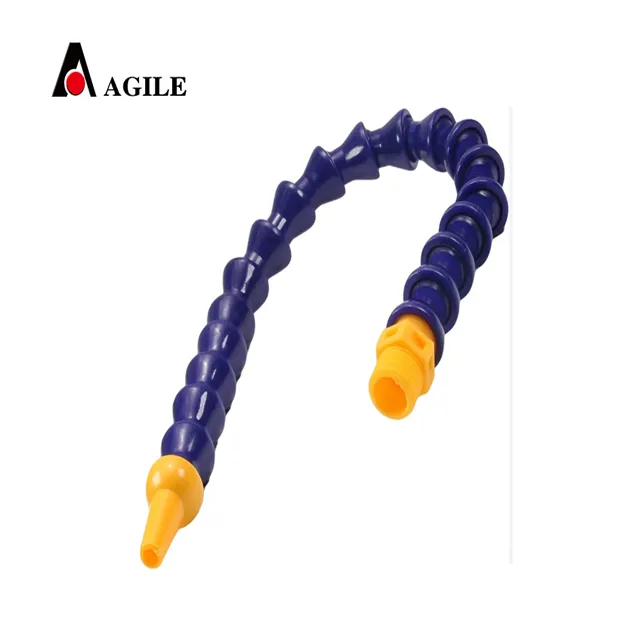
(corrugated metal conduit)
Understanding Corrugated Metal Conduit Infrastructure
Modern industrial facilities increasingly rely on robust cable protection systems to maintain operational integrity. The corrugated metal conduit
represents a critical component in these environments, offering unparalleled mechanical protection for wiring and control systems. Manufactured from high-grade stainless or galvanized steel, these flexible conduits feature helical ridges that enhance structural rigidity while maintaining bend flexibility. The spiral design increases surface area by 30% compared to smooth conduits, significantly improving heat dissipation capabilities. Industries ranging from automotive manufacturing to petrochemical plants utilize this technology to protect sensitive instrumentation cabling from crushing forces exceeding 1500 PSI.
Technical Performance Capabilities
Advanced engineering gives metal corrugated conduit remarkable physical properties. These systems maintain functionality in extreme temperatures ranging from -60°C to 450°C, with specialized alloy variants handling up to 1000°C in foundry applications. The corrugated structure provides EMI/RFI shielding effectiveness of 90dB at 1GHz, surpassing international electromagnetic compatibility standards. Laboratory testing reveals extraordinary impact resistance, withstanding 50 Joules of direct force without deformation – equivalent to a 10kg weight dropped from 500mm height. Continuous improvements in polymer coatings have extended corrosion resistance lifetimes beyond 25 years in salt spray tests per ASTM B117 standards. These properties make it ideal for integration with metal chip conveyor systems where metallic abrasives and coolants would degrade lesser materials.
Leading Industry Supplier Comparison
Manufacturer | Material Grade | Pressure Rating (PSI) | Temperature Range (°C) | Corrosion Resistance | Certifications |
---|---|---|---|---|---|
Alpha Conduit Systems | 316L Stainless | 1800 | -65 to 480 | 10,000 hr salt spray | UL, ATEX, IECEx |
Beta Shield Solutions | Hot-Dip Galvanized | 1450 | -40 to 400 | 8,000 hr salt spray | UL, CSA |
Gamma Protection Tech | 304 Stainless | 1600 | -50 to 420 | 7,500 hr salt spray | UL, RoHS |
Delta Industrial | Aluminized Steel | 1250 | -30 to 350 | 6,000 hr salt spray | ISO 9001 |
Customization Specifications
Project-specific requirements drive demand for tailored conduit solutions. Leading suppliers offer extensive customization including diameters from 12mm to 200mm with wall thicknesses varying between 0.5mm to 2.5mm. Electrical installations frequently specify anti-static versions with resistance below 10⁴ ohms, while hazardous locations require flame-retardant jackets meeting IEEE 1202 standards. For thermal management applications, composite versions featuring aerogel insulation maintain internal temperatures within ±3°C in environments ranging from -40°C to 200°C. Recent innovations include smart variants with integrated fiber optic pathways for condition monitoring, reducing installation costs by up to 40% for combined power/data runs in metal chip conveyor installations.
Industrial Deployment Scenarios
Automotive manufacturing demonstrates optimal conduit application where these systems protect sensor networks along robotic assembly lines. One BMW production facility reported 89% reduction in cable damage incidents after implementing stainless steel corrugated conduits in weld cell areas. Offshore platforms benefit from specialized marine-grade conduits that withstand saltwater immersion while protecting critical control systems; analysis shows they outperform plastic alternatives by 11x longevity in tidal zone installations. Food processing plants utilize FDA-compliant versions to prevent bacterial ingress in washdown areas. Mining operations report enhanced productivity when deploying heavy-duty conduits alongside metal chip conveyor lines, as abrasion-resistant features eliminate wiring failures from ore particulates.
Installation Methodologies
Proper installation techniques ensure optimal conduit performance. Field studies show compression fittings provide superior sealing compared to set-screw types, reducing moisture intrusion by 78%. Recommended minimum bend radius ranges from 5x to 8x conduit diameter depending on material, with specialized spring benders preventing corrugation deformation. Vertical installations exceeding 10 meters require support intervals every 1.8 meters to prevent elongation stress on connections. Implementation alongside metal chip conveyor systems demands strategic separation distances of at least 150mm to prevent vibration-induced fatigue. Recent connector innovations allow tool-free installation, reducing labor requirements by 60% on complex factory retrofits while maintaining IP69K environmental protection ratings.
Innovations in Metal Conduit Technology
Material science advancements continue enhancing corrugated metal conduit applications. New nano-ceramic coatings increase abrasion resistance by 500% while maintaining flexibility at extreme temperatures, extending service life in mineral processing operations. Sustainable manufacturing methods now reduce production energy consumption by 30% through induction heating processes. Emerging self-monitoring versions incorporate distributed fiber optic sensors that detect mechanical stress or temperature anomalies before failures occur. Industry analysts project 17% CAGR through 2028, driven by industrial automation demands requiring resilient cable protection solutions. These innovations ensure that corrugated metal conduit will remain foundational infrastructure in advanced manufacturing environments worldwide.
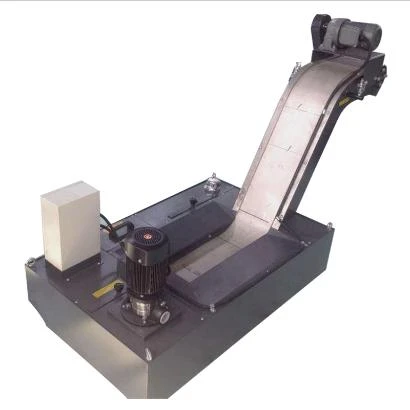
(corrugated metal conduit)
FAQS on corrugated metal conduit
Q: What is a corrugated metal conduit used for?
A: A corrugated metal conduit protects electrical cables in industrial or outdoor settings. Its flexible, ribbed structure resists physical damage and environmental factors like moisture or chemicals.
Q: How does a metal corrugated conduit differ from PVC conduits?
A: Metal corrugated conduits offer superior durability and heat resistance compared to PVC. They are ideal for high-temperature or mechanically stressful environments where plastic might fail.
Q: Can corrugated metal conduit be used with metal chip conveyor systems?
A: Yes, corrugated metal conduit is often paired with metal chip conveyor systems in manufacturing. It safeguards wiring from metal debris, vibrations, and heat generated during machining processes.
Q: What are the installation considerations for corrugated metal conduit?
A: Ensure proper bending radius to avoid kinking and use compatible fittings for airtight seals. Avoid sharp edges or abrasive surfaces that could wear down the conduit.
Q: Why choose metal corrugated conduit over rigid metal piping?
A: Metal corrugated conduit provides flexibility for complex routing without joints, reducing installation time. It also absorbs vibrations better, minimizing wear in dynamic setups.