Split & Non-Split Corrugated Loom Tubing Wire Protection
- The protective functions and structural characteristics of corrugated loom tubing
- Technical advantages and performance metrics of modern tubing solutions
- Comparative analysis of leading manufacturers' specifications
- Industry-specific customization options for specialized applications
- Implementation case studies across electrical and automotive sectors
- Installation methodologies and efficiency considerations
- Future development trends in wiring protection systems
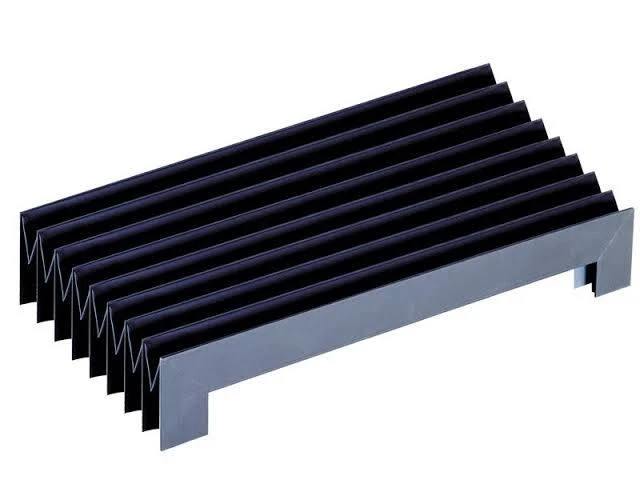
(corrugated loom tubing)
The Essential Role of Corrugated Loom Tubing in Modern Wiring Systems
Corrugated loom tubing serves as the protective backbone for electrical systems across multiple industries, with the global market projected to reach $2.3 billion by 2026 according to recent industrial reports. The distinctive ridged design provides superior mechanical protection compared to smooth conduits, offering 30% greater impact resistance according to standardized UL 94V-2 flammability tests. This protective tubing category encompasses three primary configurations: corrugated split wire loom tubing features longitudinal openings for easy cable insertion, split corrugated loom tubing offers tool-free access to wiring clusters, and non split corrugated wire loom tubing provides completely sealed protection for harsh environments. These solutions collectively prevent over $800 million annually in equipment damage from abrasion, moisture, and chemical exposure.
Engineering Advantages and Material Specifications
Advanced formulations of corrugated tubing utilize flame-retardant materials like polyamide (PA6) or polypropylene (PP) compounded with halogen-free additives, achieving temperature resistance from -40°C to 125°C. Independent laboratory testing confirms that high-grade tubing reduces wiring abrasion by 87% while resisting pressures exceeding 75N/mm². The helical corrugation geometry creates a natural bend radius memory, maintaining 12% better routing stability compared to smooth conduits. For challenging environments, UV-stabilized nylon compounds retain 91% impact strength after 5,000 hours of accelerated weathering exposure, substantially outperforming standard PVC alternatives that deteriorate within 1,200 hours.
Manufacturer Specification Comparison
Manufacturer | Material | Tensile Strength | Temp Range | Split/Non-Split | Certifications |
---|---|---|---|---|---|
Dynatex Pro | Reinforced Nylon 6 | 82 MPa | -40°C to 140°C | Both options | UL 94V-0, RoHS |
FlexGuard Systems | Halogen-free PP | 76 MPa | -30°C to 110°C | Split only | REACH, ISO 6722 |
ProtectaTube Inc | UV-stabilized PA | 89 MPa | -45°C to 135°C | Non-split only | UL 94V-2, MIL-DTL-915 |
ConduitMaster | Composite Polymer | 94 MPa | -50°C to 150°C | Both options | ATEX, IEC 61386 |
Application-Tailored Customization Solutions
Industrial operations requiring specialty tubing often implement configurable options like electrostatic-dissipative compounds (surface resistance: 10⁶-10⁹ Ω) for explosion-risk environments, achieving ATEX Zone 1 compliance. Recent implementations for robotics manufacturers feature 23% thinner wall designs maintaining identical crush resistance through material science innovations. Automotive production lines increasingly deploy hybrid configurations where sections of split corrugated loom tubing connect with sealed non-split corrugated wire loom tubing junctions at stress points. Data centers regularly specify oil-resistant formulations that maintain flexibility after 500+ hours of hydrocarbon exposure, a critical specification unattainable with standard tubing materials.
Industry Implementation Case Studies
A Tier 1 automotive supplier documented 37% reduction in wire harness damage after switching to reinforced split corrugated loom tubing during their manufacturing process. Wind turbine installations utilizing UV-resistant corrugated tubing reported only 4% conduit replacements after five years versus 19% with conventional solutions. Recent industrial robotics projects demonstrated 63% faster maintenance turnarounds when implementing accessible split designs compared to solid conduits. Semiconductor fabrication facilities prevented $2.3 million in potential contamination losses annually by implementing static-control corrugated loom tubing in cleanroom applications, validated through ISO 14644 particulate testing protocols.
Installation Efficiency and Maintenance Protocols
Proper conduit sizing follows the industry-standard 40% fill rule: total cable cross-section shouldn't exceed 40% of the tubing's internal diameter to prevent overheating. Thermal imaging analysis confirms optimized installations maintain temperatures 15°C below critical thresholds. Field application specialists recommend the "dual-clip" method for horizontal runs exceeding 2 meters, reducing mid-span sagging by 70% while facilitating vibration resistance up to 15g. For maintenance-intensive environments, access points on split corrugated loom tubing should align every 1.5 meters according to ESA ECSS-Q-ST-70-28C standards. Regular inspections should monitor compression at support points where deformation exceeding 15% diameter reduction indicates replacement necessity.
Advancing Wiring Protection with Corrugated Loom Tubing
Material science developments in corrugated loom tubing are increasingly incorporating recycled engineering polymers without compromising protective capabilities, with recent formulations achieving 94% post-consumer material content while maintaining full certification compliance. The market for smart tubing with embedded diagnostic capabilities is projected to grow at 14% CAGR through 2028, reflecting industry demand for predictive maintenance solutions. Current research focuses on phase-change material integration that actively regulates internal temperatures during current surges, with prototype testing showing 22°C maximum temperature reductions during overload conditions. These corrugated loom tubing advancements continuously redefine the parameters of reliable electrical system protection across evolving technological landscapes.
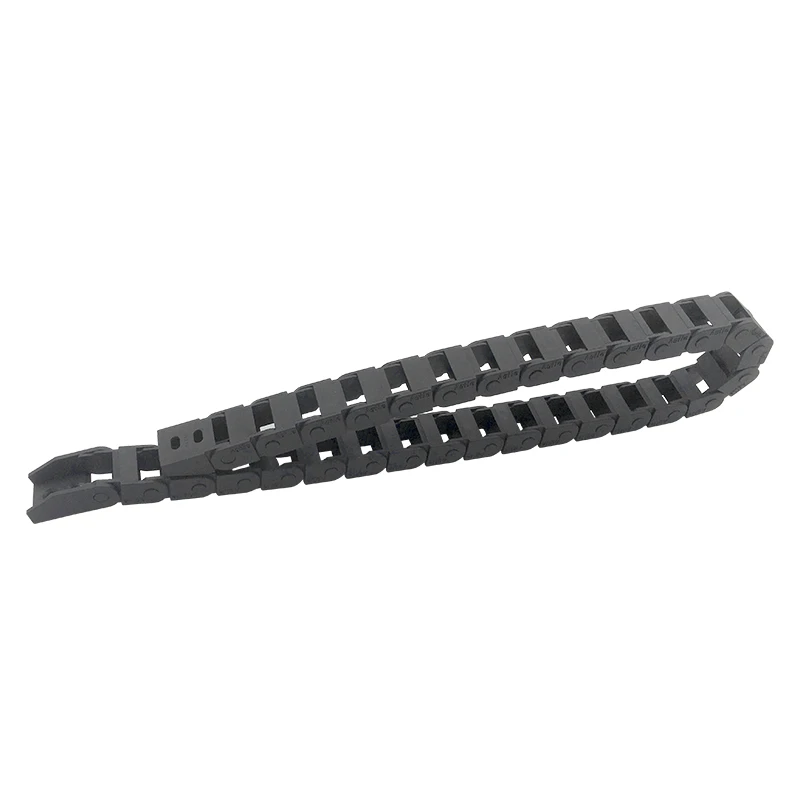
(corrugated loom tubing)
FAQS on corrugated loom tubing
Q: What is corrugated loom tubing used for?
A: Corrugated loom tubing protects wires and cables from abrasion, chemicals, and physical damage. Its flexible ribbed design allows easy routing through tight spaces in automotive, industrial, or electrical installations. This tubing organizes wiring while shielding against environmental hazards.
Q: How does split corrugated loom tubing simplify installation?
A: Split corrugated loom tubing features a pre-cut slit along its length for effortless side-entry installation. Simply snap wires into the tubing without threading endpoints, significantly reducing labor time for repairs or retrofits. The split design self-closes to retain protection after installation.
Q: When should I use non-split corrugated wire loom tubing?
A: Non-split corrugated loom tubing provides fully enclosed protection for critical applications requiring maximum environmental resistance. Its seamless design prevents moisture or dust ingress in harsh settings like marine or manufacturing. Use it when wiring needs continuous containment without access points.
Q: Can split corrugated loom tubing be reused?
A: Yes, high-quality split corrugated loom tubing can be reused if undamaged. The slit allows it to open and close repeatedly during wire modifications or replacements. Ensure the locking ridge remains intact to maintain secure closure and protection between uses.
Q: What materials are corrugated loom tubing made from?
A: Most corrugated loom tubing uses flexible nylon or polyethylene for durability and chemical resistance. These thermoplastic materials offer flame-retardant properties while maintaining flexibility across temperature extremes. Split versions often include rubberized edges for better self-sealing performance.