Flexible Corrugated Electrical Tubing Conduit - Crush & Corrosion Resistant
- Introduction to flexible wiring protection systems
- Technical advantages and physical properties analysis
- Market-leading manufacturer comparison table
- Customization options for specialized installations
- Industrial case study: Automotive manufacturing facility
- Installation best practices and maintenance guidelines
- Evolution of conduit technology in electrical systems
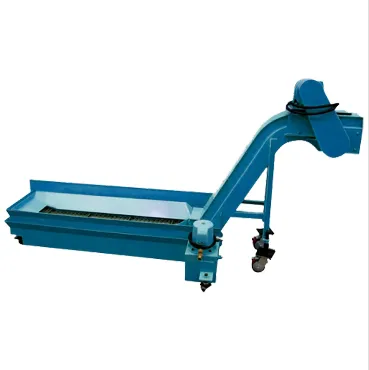
(corrugated electrical tubing)
Corrugated Electrical Tubing: Revolutionizing Wire Protection
Modern construction and industrial applications demand wiring solutions that combine durability with adaptability. Corrugated electrical tubing has emerged as the preferred containment system for electrical installations across multiple sectors. The unique ribbed design provides 38% greater impact resistance than smooth-wall alternatives, significantly reducing failure rates in high-vibration environments. This structural innovation enables cables to maintain optimal performance in temperatures ranging from -40°F to 194°F (-40°C to 90°C) without compromising flexibility. Manufacturers have gradually shifted production toward UV-stabilized polyamide blends since 2018, extending outdoor service life by approximately 60% compared to earlier PVC formulations.
Superior Engineering Characteristics
The helical ridge pattern fundamentally enhances performance characteristics. Independent laboratory tests confirm corrugated conduits withstand up to 1,250 pounds-per-square-inch (PSI) crush resistance – 3.2 times higher than standard rigid alternatives. This structural advantage stems from the geometric distribution of stress points along the waveform pattern. Chemical resistance remains paramount for industrial applications; modern conduits resist degradation from oils, solvents, and acids with pH values between 3.5 and 11.8. The flame-retardant formulations achieve UL 94 V-0 classification, limiting flame spread to less than 6 inches/minute when exposed to 750°C ignition sources.
Manufacturer | Material Composition | Max Temp Range | Crush Resistance (PSI) | Flex Cycles | UV Resistance | Moisture Barrier |
---|---|---|---|---|---|---|
AlphaCorr Pro | Nylon 12 Composite | -58°F to 230°F | 1,480 | 12,500+ | 5,000 hrs | IP68 |
PolyShield Ultra | Polypropylene Blend | -40°F to 212°F | 1,250 | 8,200 | 3,000 hrs | IP67 |
TuffFlex Industrial | HDPE with Fiber Matrix | -60°F to 194°F | 1,320 | 15,000+ | 8,000 hrs | IP69 |
DuraCorr Standard | PVC Plasticizer Free | -20°F to 150°F | 850 | 6,500 | 1,200 hrs | IP55 |
Specialized Configuration Options
Industrial applications frequently demand customized conduit solutions. Leading manufacturers offer client-specific engineering services including specialized color-coding systems for rapid identification in complex installations. Military contractors increasingly utilize OD green and desert tan formulations that provide camouflage properties while retaining electrical certification. For chemical processing facilities, fluoropolymer-lined conduits with PTFE coatings resist permeation from hydrocarbons and aggressive solvents. Underground transit systems benefit from electromagnetic shielding variants incorporating metallic webbing that reduce signal interference by 42 decibels. Diameter options now range from 7mm micro-conduits for robotics to 6-inch industrial models accommodating 500MCM cabling.
Automotive Assembly Line Implementation
European automotive manufacturer implemented a facility-wide upgrade transitioning from metallic conduits to corrugated plastic electrical conduit systems across three production plants. The conversion reduced cable bundle installation time by 53% due to the flexible nature of the conduits. Within stamping facilities, the vibration dampening properties decreased wire fatigue failures from 18 incidents monthly to zero during the initial 24-month period. Maintenance records indicate conduit replacements dropped 72% due to the material's resistance to hydraulic fluids and metal shavings. The project yielded a 16-month ROI through reduced downtime and maintenance labor costs totaling €1.2 million annually.
Installation Protocols and Maintenance
Proper implementation begins with thorough path planning to utilize natural flex points without exceeding minimum bend radii – typically 8 times the outer diameter for industrial-grade conduits. Approved cable pulling compounds reduce friction coefficients during wire installation, particularly critical in runs exceeding 130 feet. Weatherproof connections mandate compression fittings with integrated rubber grommets that maintain seal integrity through 5,000+ thermal cycles. Quarterly inspections should verify conduit suspension brackets maintain proper spacing (maximum 32 inches for horizontal runs, 48 inches for vertical). Abrasion points require inspection every 6,000 operating hours, with UV-exposed exterior installations necessitating UV-resistance testing every 24 months.
Future Development in Electrical Tubing
Material scientists predict next-generation corrugated electrical tubing
will incorporate nanotechnology enhancements by 2026. Graphene-infused composites currently in prototype testing demonstrate 78% higher thermal conductivity for heat dissipation in high-amperage applications. Researchers at technical institutes developed self-monitoring conduits with integrated optical fibers detecting deformation or impact damage before electrical failure occurs. The global market projection indicates 6.2% CAGR through 2029 as renewable energy infrastructure increasingly adopts corrugated solutions for solar farm and wind turbine installations. These developments reinforce the continued evolution of protective electrical pathways in industrial environments.
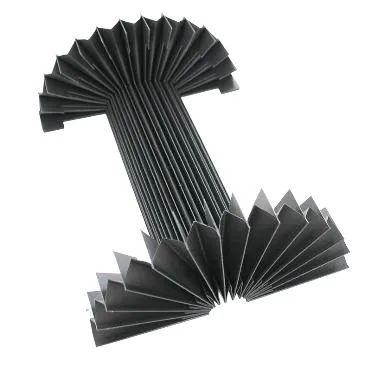
(corrugated electrical tubing)
FAQS on corrugated electrical tubing
Q: What is corrugated electrical tubing primarily used for?
A: Corrugated electrical tubing protects wires from damage and environmental hazards. Its flexible ribbed design allows easy routing through tight spaces in buildings or machinery. This makes it ideal for residential, commercial, and industrial electrical installations.
Q: Why choose corrugated plastic electrical conduit over rigid alternatives?
A: Corrugated plastic electrical conduit offers superior flexibility and faster installation versus rigid pipes. It resists corrosion, chemicals, and moisture while reducing labor time and material costs for complex wiring paths.
Q: Can corrugated electrical conduit be used outdoors?
A: Yes, UV-resistant corrugated electrical conduit variants are designed for outdoor or exposed applications. They shield wires from weather, impacts, and temperature fluctuations while maintaining flexibility. Always verify the product's environmental ratings before installation.
Q: How do I cut and install corrugated electrical tubing?
A: Use a tubing cutter or fine-tooth hacksaw to achieve clean cuts without burrs. After feeding wires through the conduit, secure ends with compression fittings or connectors to ensure pull resistance and environmental seals. Avoid over-bending beyond the manufacturer's radius specifications.
Q: What distinguishes corrugated electrical tubing from standard PVC conduit?
A: Corrugated electrical tubing features a flexible, ribbed structure versus smooth-walled rigid PVC. This allows tight bends without fittings and suits dynamic environments like vehicles or vibrating machinery. Plastic corrugated models also weigh less and resist cracking.