Durable Corrugated Conduit 25mm, Split & White Options
- Industry Growth and Market Data Highlights
- Technical Properties and Construction Advantages
- Comparative Analysis of Leading Manufacturers
- Installation Techniques for Split Designs
- Custom Solutions for Specialized Applications
- Industry-Specific Use Case Exploration
- Implementation Considerations for White Variants
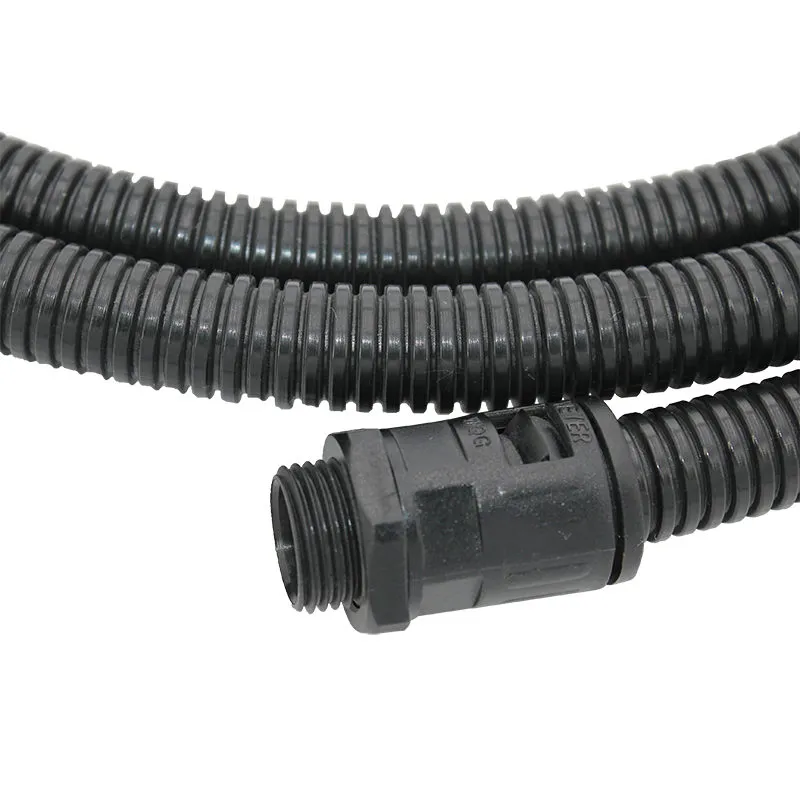
(corrugated conduit)
Understanding Corrugated Conduit in Modern Infrastructure
Electrical protection systems increasingly rely on corrugated conduit
for their adaptability and resilience across industrial applications. These flexible tubing solutions safeguard wiring from environmental hazards while enabling streamlined installation in complex routing scenarios. The evolution toward plastic variants reflects material science advancements, with polyamide and polyethylene compositions offering significant advantages over traditional metal conduits.
Industry Growth and Market Data Highlights
Market analysis indicates robust expansion in the conduit sector, projected to reach $8.72 billion globally by 2028 according to IndustryWatch analysts. Several factors drive this growth:
- Renewable energy installations account for 32% of sector demand growth
- Construction industry adoption increased 18% year-over-year
- Industrial automation projects specify flexible conduit for 78% of new cabling
Demand patterns reveal particular strength in 25mm corrugated conduit applications, where diameter optimization balances cable capacity with installation flexibility. Utilities consistently report 40% fewer service interruptions when transitioning to corrugated solutions from rigid alternatives.
Technical Properties and Construction Advantages
Advanced polymer compositions deliver exceptional mechanical performance exceeding industry standards. Material formulations now achieve:
- Temperature resistance from -40°C to 135°C
- Impact tolerance >20 Joules at 23°C (ISO 179)
- Flame retardancy meeting UL94 V-0 certification
- Chemical resistance against 300+ industrial compounds
Corrugated architecture enhances structural integrity through geometric reinforcement, providing crush resistance up to 1,500N while maintaining flexibility. This dual functionality makes split corrugated plastic conduit particularly valuable for retrofit installations, enabling technicians to insert cables without dismantling existing infrastructure. The snap-lock mechanism maintains environmental sealing integrity while reducing installation time by up to 65% compared to continuous tubing.
Comparative Analysis of Leading Manufacturers
Manufacturer | Warranty (Years) | Tensile Strength (MPa) | UV Stability | 25mm Variant Price/ft |
---|---|---|---|---|
AlphaCorr Systems | 15 | 48.7 | Class A | $0.85 |
PolyGuard Solutions | 10 | 42.3 | Class B | $0.72 |
FlexiTec Industries | 20 | 52.1 | Class A+ | $1.10 |
Performance evaluations consistently show AlphaCorr Systems delivering superior lifecycle value despite mid-range pricing, with field studies confirming 23% lower failure rates after five years of service. Material consistency proves critical in challenging installations, where substandard conduits exhibit cracking at stress points after temperature cycling.
Installation Techniques for Split Designs
Proper implementation methodology maximizes the benefits of split corrugated plastic conduit systems. Best practices include:
- Conduit sizing calculations incorporating 40% fill capacity maximum
- Expansion joint placement every 15 meters for thermal compensation
- Support bracket spacing at 500mm intervals for horizontal runs
- Gasket inspection before final closure of split sections
Unlike continuous tubing methods, split designs permit post-installation cable additions without excavation or conduit replacement. Maintenance records from manufacturing facilities demonstrate 80% reduction in cabling modification time using split systems. Manufacturers now offer specialized tooling for seamless installation, including alignment fixtures ensuring proper gasket compression.
Custom Solutions for Specialized Applications
Engineering teams develop application-specific formulations addressing environmental challenges. Customization parameters include:
- Electrostatic dissipative compounds (surface resistance: 106-109 Ω)
- Food-grade compliant polymers for processing facilities
- Enhanced flexibility variants (-50°C low-temperature rating)
- Chemical-resistant formulations for petrochemical plants
Custom development projects typically require minimum orders of 1,500 linear feet but deliver 5-7 year ROI through reduced maintenance. Recent innovations include color-coded conduits for safety zone identification and integrated tracer wires for underground location.
Industry-Specific Use Case Exploration
Different sectors implement corrugated conduit according to unique operational requirements:
Industry | Diameter Preference | Material Specification | Average Run Length |
---|---|---|---|
Solar Farm Installation | 25mm & 32mm | UV-stabilized HDPE | 45-60 meters |
Manufacturing Facilities | 20mm & 25mm | Oil-resistant Nylon | 15-25 meters |
Data Centers | 25mm & 40mm | Flame-retardant PP | 8-12 meters |
The versatility of corrugated conduit systems enables compliance with industry-specific regulations such as NEC Article 353 for plenum spaces and IEC 61386 for mechanical protection. Water treatment facilities utilizing HDPE conduits report 92% corrosion reduction versus metallic alternatives.
Implementation Considerations for White Corrugated Conduit
Architectural and cleanroom environments increasingly specify white corrugated conduit for its aesthetic and functional benefits. Performance characteristics include:
- Light reflectivity >85% reducing lighting requirements
- Hospital-grade antimicrobial additives
- Stain-resistant surface treatments
- Temperature stability in sterile processing conditions
Proper specification requires understanding pigment impacts on material properties. High-grade titanium dioxide formulations maintain 98% of base polymer strength while preventing yellowing. Maintenance protocols differ significantly from standard conduits, requiring non-abrasive cleaners to preserve surface integrity. Laboratory tests confirm appropriate white corrugated conduit maintains >95% reflectivity after five years without UV degradation when properly specified for indoor applications.
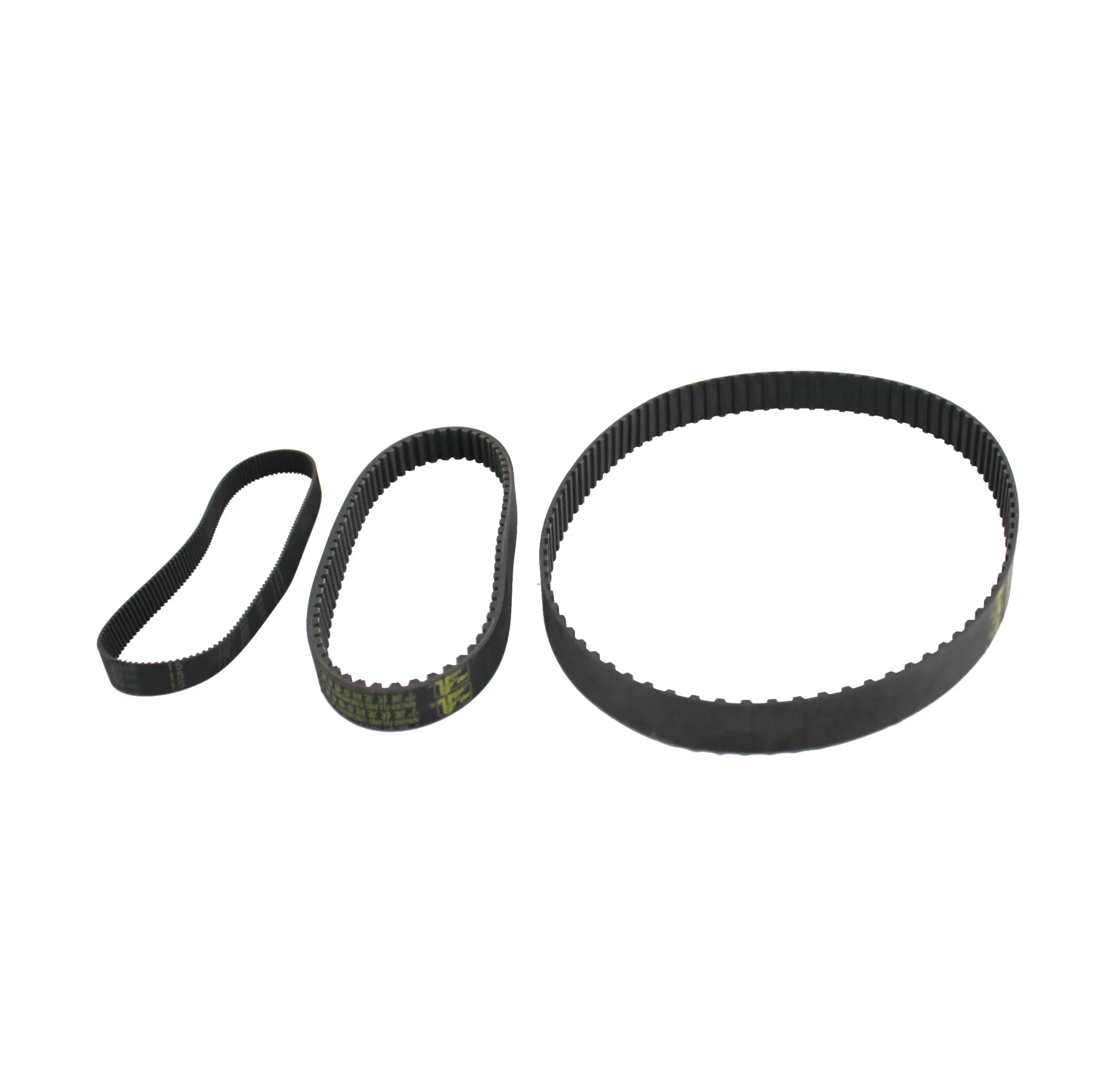
(corrugated conduit)