Comprehensive Guide to Selecting the Right Size Cable Drag Chains for Your Applications
Understanding Cable Drag Chain Size Chart A Comprehensive Guide
In various industries, the efficient management of cables and hoses is crucial for maintaining operational efficiency and safety. One vital component that facilitates this process is the cable drag chain, also known as cable carrier or energy chain. It helps organize and protect cables and hoses that move with machinery, ensuring that they remain tangle-free and safeguarded from wear and tear. A fundamental aspect of selecting the right cable drag chain is understanding the size chart, which provides crucial information for proper installation and functionality.
Cable drag chains come in various sizes, which are typically defined by their inner width and height. The size of the chain is critical because it determines the number and type of cables it can effectively handle. A well-structured size chart allows users to select the appropriate drag chain based on the size and number of cables they need to accommodate. Each entry in the chart outlines dimensions, load capacity, and the maximum bend radius, which helps users find a matching drag chain for their specific applications.
The size chart typically includes two primary dimensions the inner width (IW) and the inner height (IH). The IW indicates the maximum width of the cables that can fit side by side within the carrier, while the IH denotes the vertical space available for taller components. Depending on the application, it’s essential to choose a chain with slightly larger dimensions than the actual size of the bundled cables, allowing for adequate movement and reducing friction.
cable drag chain size chart
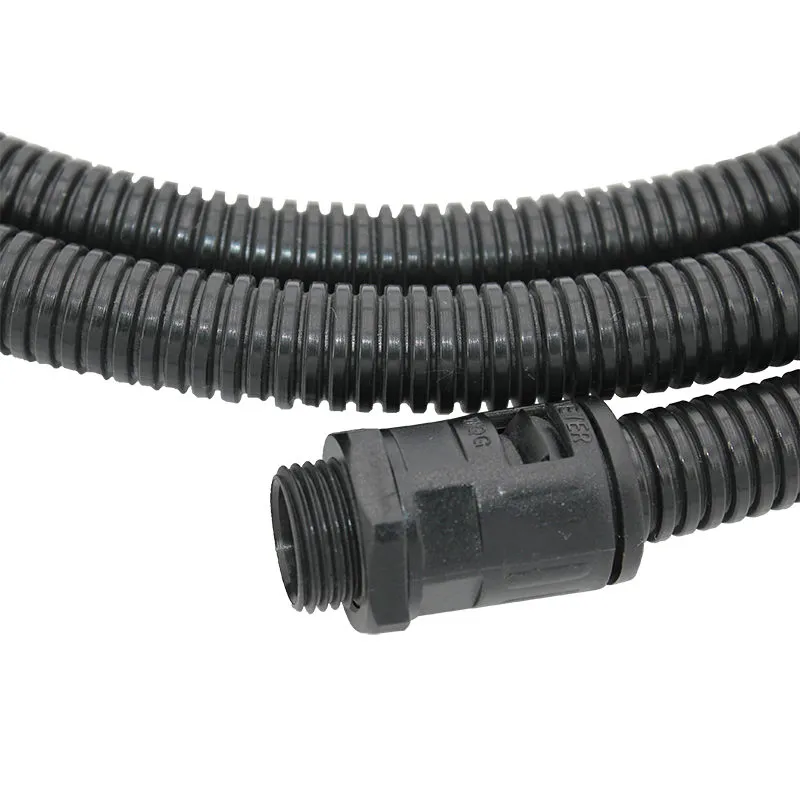
In addition to IW and IH, the cable drag chain size chart often features load capacity information. This measurement indicates how much weight the chain can bear while in motion, ensuring that users select a drag chain capable of handling the operational demands of their machinery. Additionally, users should pay attention to the maximum bend radius (MBR), which is crucial for dynamic applications where the chain must curve around corners or bend during operation. If the bend radius is too sharp, it can lead to cable damage or chain failure.
When consulting a cable drag chain size chart, it is also vital to consider the operating environment. Factors such as temperature, humidity, and exposure to chemicals can influence the type of material used in the construction of the drag chain. For instance, stainless steel or reinforced nylon chains may be more suitable for environments prone to corrosion or wear. This ensures not only the longevity of the drag chains but also the cables they protect.
Moreover, the installation process of the cable drag chain can also affect its size selection. Proper installation aligns the drag chain with the moving parts of the machinery while providing support for the cables within it. It is essential to account for mounting brackets, supports, and any additional space requirements based on how the drag chain is integrated into the system.
In conclusion, the cable drag chain size chart serves as an invaluable resource in the selection process. By understanding the key dimensions—inner width and height, load capacity, and maximum bend radius—users can make informed decisions that enhance the efficiency and safety of their operations. Properly sized drag chains extend the lifespan of cables and hoses, reduce maintenance costs, and ensure that machinery operates smoothly. As industries continue to evolve, the importance of selecting the right cable management solutions will remain a critical factor in engineering and design. Always consult the size chart to make the best choice for your specific applications, and ensure operational integrity for years to come.