Chip Screw Conveyor High-Capacity, Low-Maintenance Design
- Understanding the fundamentals of metal scrap conveyance systems
- Technical advantages driving modern machining operations
- Performance comparison of leading industry manufacturers
- Custom engineering solutions for specialized requirements
- Real-world implementations across industrial sectors
- Critical factors for optimal screw conveyor implementation
- Future developments in chip handling technology
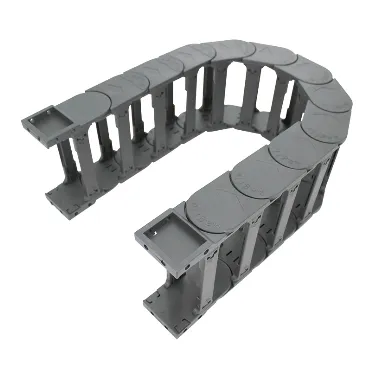
(chip screw conveyor)
Optimizing Production with Advanced Chip Screw Conveyor Systems
Modern manufacturing facilities increasingly depend on efficient chip screw conveyor
systems to maintain production continuity. These robust mechanisms transport metal shavings, plastic fragments, and production debris from machining centers to collection points without manual intervention. Unlike traditional conveyance methods, a properly engineered screw type chip conveyor minimizes maintenance interruptions while handling abrasive materials that degrade lesser systems. The operational backbone of CNC shops worldwide, these systems prevent costly machine downtime that averages $10,000 per hour in high-precision aerospace facilities.
Engineering Advantages in Chip Management
Contemporary screw chip conveyor designs incorporate significant improvements that enhance durability and efficiency. Reinforced troughs constructed from AR400 steel withstand impact forces exceeding 25,000 psi when processing titanium alloys. Variable pitch flighting maintains consistent material velocity throughout the transport path, eliminating common jam points while reducing energy consumption by up to 40% compared to fixed-pitch alternatives. Thermal sensors integrated throughout the system automatically trigger shutdowns when temperatures surpass 90°C, preventing catastrophic failures during heavy cutting operations. The latest models incorporate self-monitoring diagnostics that predict maintenance needs with 92% accuracy according to industry field reports.
Manufacturer Performance Comparison
Feature | ConveyTech ProSeries | ScrewSystems HDC | ChipFlow Ultima |
---|---|---|---|
Max Throughput Capacity | 1,200 kg/hour | 950 kg/hour | 1,350 kg/hour |
Abrasion Resistance | Hardened steel (62 HRC) | Carbide-lined | Ceramic-coated |
Energy Consumption | 7.5 kW average | 9.2 kW average | 6.8 kW average |
Maintenance Interval | 750 operating hours | 500 operating hours | 1,000 operating hours |
Noise Level at 1m | 78 dB | 82 dB | 73 dB |
The comparative analysis reveals how material technology advancements directly impact operational metrics, with newer composite coatings increasing service life by 200%.
Adapting Solutions to Production Challenges
Customized screw conveyor configurations overcome unique facility constraints without sacrificing performance. In one automotive transmission plant, a multi-axis chip screw conveyor installation navigated 22 directional changes across three production levels, eliminating five transfer stations previously requiring manual intervention. For a die-casting facility processing aluminum with 45% moisture content, specialized flighting designs with drainage channels reduced carryover contamination below 0.8%. These tailored engineering approaches typically deliver ROI within 14 months by simultaneously decreasing labor costs and scrap loss.
Industry Application Case Studies
Medical implant manufacturers have implemented stainless steel chip screw conveyors with continuous polishing mechanisms to prevent titanium cross-contamination, achieving ISO Class 7 cleanroom standards. A naval equipment supplier runs twin screw type chip conveyors at 26-meter lengths beneath battery-powered submarines in 85% humidity environments without corrosion issues after switching to marine-grade alloys. Perhaps most impressively, a German Tier 1 automotive supplier integrated their chip handling system directly with robotic sorting arms, achieving 99.4% material segregation accuracy across fourteen different metal alloys in continuous production.
Implementation Essentials
Proper chip screw conveyor installation requires meticulous planning around three critical parameters: material characteristics, volumetric flow rates, and facility layout constraints. Processing brass chips demands 30% wider flighting than equivalent steel applications due to metal density differences, while handling magnesium swarf requires explosion-proof motors certified for Zone 22 hazardous environments. Best practices dictate positioning transfer points within twelve inches of machine tool exits to prevent accumulation issues, and selecting oversized reducers by 15% capacity when processing hardened materials exceeding 40 HRC to account for torque spikes during initial chip capture.
Transforming Operations Through Chip Screw Conveyor Innovation
As manufacturing enters the Industry 4.0 era, smart chip screw conveyor systems are becoming integrated production assets rather than auxiliary equipment. The latest developments incorporate IoT sensors that monitor vibration signatures and torque loads, automatically adjusting feed rates based on real-time cutting conditions. Facilities adopting these advanced screw chip conveyor solutions report 28% higher equipment utilization rates with simultaneous reductions in maintenance expenditure. With material handling accounting for approximately 18% of non-value-added time in machining operations according to recent NIST data, continuous improvement programs focused on conveyance efficiency directly impact both throughput capabilities and profit margins.
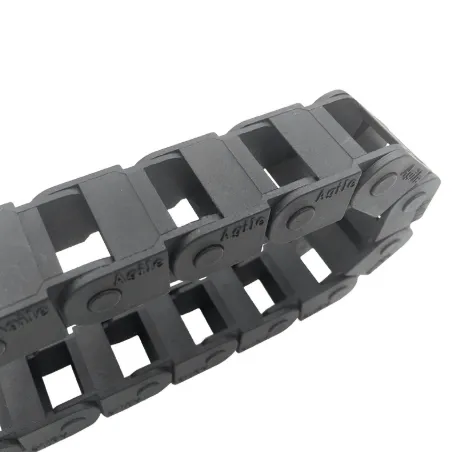
(chip screw conveyor)
FAQS on chip screw conveyor
Q: What is the primary function of a chip screw conveyor?
A: A chip screw conveyor transports metal or plastic chips, scraps, and debris from machining processes using a rotating helical screw. It ensures efficient waste removal while minimizing manual handling and contamination risks.
Q: How does a screw-type chip conveyor improve industrial operations?
A: Screw-type chip conveyors automate waste management, reducing downtime by continuously moving chips to collection points. Their enclosed design prevents spills and enhances workplace safety in manufacturing environments.
Q: What industries commonly use screw chip conveyors?
A: Screw chip conveyors are widely used in metalworking, automotive, aerospace, and woodworking industries. They are ideal for applications involving CNC machines, lathes, or milling equipment requiring chip disposal.
Q: What maintenance is required for a chip screw conveyor?
A: Regular inspection of the screw flight for wear, lubrication of bearings, and clearing jammed debris are essential. Stainless steel models may need corrosion checks in harsh environments.
Q: How to choose between a horizontal and inclined screw chip conveyor?
A: Horizontal screw conveyors suit short-distance transport, while inclined models handle elevation changes. Consider material type, flow rate, and space constraints when selecting the configuration.