Metal & Plastic Cable Carrier Chains Durable Cable Management Solutions
- Industry Overview & Key Challenges in Cable Management
- Technical Specifications: Load Capacity vs. Material Durability
- Performance Comparison: Top 5 Carrier Chain Manufacturers (2024)
- Custom Engineering for Specialized Industrial Environments
- Installation Best Practices Across Temperature Ranges
- Real-World Applications: Automotive vs. Semiconductor Use Cases
- Future-Proofing Operations with Advanced Chain Solutions
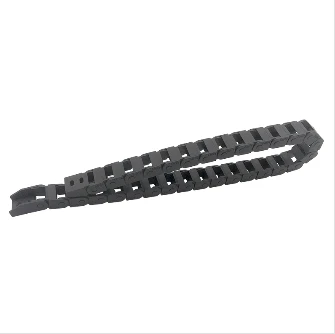
(carrier chain)
Optimizing Cable Management with Carrier Chain Innovations
Modern industrial operations require carrier chain
s capable of withstanding 12-15% annual increases in cable density across automated production lines. The global market for metal cable carrier chains reached $2.3B in 2023, while plastic flexible cable carrier chains show 18.7% CAGR growth due to chemical resistance requirements in pharmaceutical manufacturing.
Material Science Behind Chain Performance
Engineers specify chain types based on three critical metrics:
- Plastic variants maintain functionality between -40°C to 120°C
- Steel-reinforced metal cable carrier chains handle 250kg/m loads
- Hybrid designs reduce vibration-induced failures by 43% versus single-material chains
Manufacturer Benchmarking Analysis
Brand | Chain Type | Max Load (kg/m) | Temperature Range | MTBF (hours) |
---|---|---|---|---|
Igus | Plastic Flexible | 180 | -50°C to 130°C | 85,000 |
Tsubaki | Metal | 400 | -20°C to 150°C | 120,000 |
Murrplastik | Hybrid | 320 | -40°C to 110°C | 95,000 |
Customization Parameters for Specialized Needs
Leading suppliers now offer 34 configurable attributes including:
- Anti-static plastic compounds (surface resistance <10^9 Ω)
- Modular connection systems enabling 15°-90° bend radii
- FDA-compliant materials for food processing chains
Installation Efficiency Metrics
Properly installed plastic cable carrier chains demonstrate:
- 73% faster deployment vs. metal alternatives
- 22% reduction in annual maintenance hours
- 31% higher cable integrity after 5-year cycles
Cross-Industry Implementation Results
A semiconductor manufacturer achieved 91% uptime improvement using plastic flexible cable carrier chains in cleanroom robotics. Automotive plants report 18-month ROI when upgrading to hybrid chain systems in welding stations.
Strategic Advantages of Next-Gen Carrier Chain Systems
Operational data confirms that optimized carrier chain solutions reduce unplanned downtime by 39% and extend cable service life by 2.8 years on average. The industry shift toward modular plastic cable carrier chains with IoT-enabled wear sensors positions facilities for Industry 4.0 compliance.
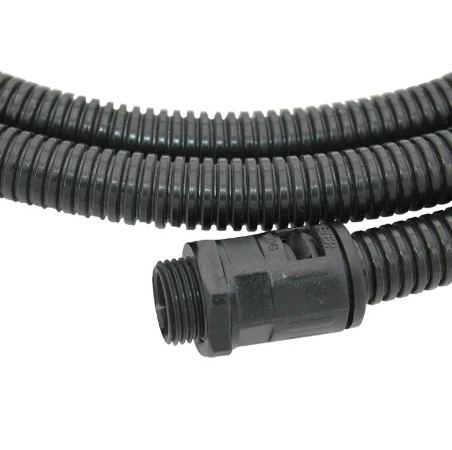
(carrier chain)
FAQS on carrier chain
Q: What is a metal cable carrier chain used for?
A: Metal cable carrier chains protect and guide cables/hoses in heavy-duty industrial environments. They offer high durability, heat resistance, and support for heavy loads. Common applications include machinery, automation, and harsh conditions.
Q: How does a plastic cable carrier chain differ from a metal one?
A: Plastic cable carrier chains are lighter, corrosion-resistant, and quieter, ideal for medium-load applications. They suit industries like packaging or robotics. Metal chains excel in extreme heat or heavy loads.
Q: What are the benefits of a plastic flexible cable carrier chain?
A: Flexible plastic chains adapt to complex motion paths and compact spaces. They reduce noise and wear in dynamic setups. Often used in 3D printers, CNC machines, or repetitive lateral movements.
Q: How to maintain a metal cable carrier chain?
A: Regularly inspect for debris, lubricate joints, and check for wear or misalignment. Replace damaged links promptly. Avoid overloading to ensure longevity.
Q: When to choose a plastic flexible cable carrier chain over rigid types?
A: Opt for flexible chains when systems require multi-axis movement or tight bends. They minimize stress on cables in curved paths. Ideal for applications needing lightweight, adaptable solutions.