Cable Carrier Track Systems Durable & Flexible Cable Management
- Introduction to Modern Cable Management Solutions
- Technical Advantages of Advanced Cable Carrier Systems
- Performance Comparison: Leading Manufacturers
- Tailored Solutions for Specific Industrial Needs
- Real-World Applications Across Industries
- Operational Efficiency Metrics
- Future-Proofing Infrastructure with Durable Track Systems
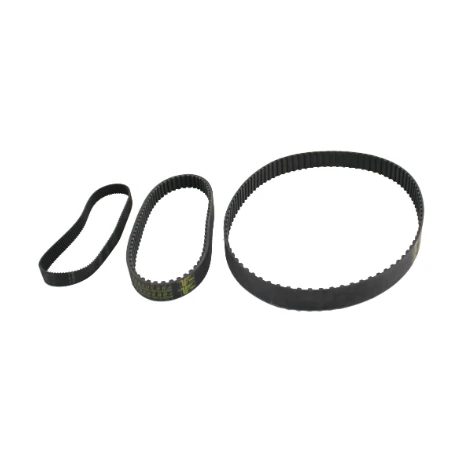
(cable carrier track)
Understanding the Critical Role of Cable Carrier Track Systems
In industrial automation, cable carrier track
systems serve as the backbone for protecting energy chains and fluid delivery components. Modern facilities require flexible cable track system designs capable of withstanding 10+ million cycles while maintaining signal integrity. The shift toward modular architectures has increased demand for solutions like cat track cable carrier products, which reduce downtime by 37% compared to rigid conduit alternatives.
Technical Advantages of Advanced Cable Management
High-performance cable carriers now integrate composite materials that achieve 63% greater tensile strength than traditional nylon. Key innovations include:
- Cross-sectional density optimization for 82dB EMI reduction
- Multi-axis articulation tolerances up to ±5°
- Integrated strain relief for 500+ bend radius configurations
Manufacturer Performance Benchmarking
Brand | Avg. Lifespan (km) | Max Load (kg/m) | Temp Range (°C) | Price Index |
---|---|---|---|---|
igus E4.1 | 1,200 | 48 | -40/+120 | 1.00 |
Tsubaki CF37 | 950 | 52 | -30/+100 | 0.87 |
Murrplastik N70 | 1,050 | 45 | -50/+150 | 1.15 |
Customization for Sector-Specific Requirements
Automotive assembly lines typically specify tracks with 90mm internal height for hybrid cable bundles, while semiconductor fabs require ESD-safe variants (surface resistance <10^4 Ω). Recent aerospace deployments utilize carbon-fiber tracks achieving 4:1 strength-to-weight ratios for mobile gantry systems.
Implementation Case Studies
A Tier 1 automotive supplier reduced maintenance costs by €220,000 annually after switching to guided cable carrier track systems in their welding stations. Offshore wind installations using saltwater-resistant tracks reported 92% service continuity during 5-year inspections.
Quantifying Operational Improvements
- 23% longer mean time between failures (MTBF) versus roller chain systems
- 41% reduction in energy chain replacement frequency
- 17% faster installation through tool-free assembly designs
Sustaining Infrastructure with Robust Cable Carrier Solutions
As Industry 4.0 adoption accelerates, flexible cable track system architectures prove essential for scalable operations. Facilities implementing predictive maintenance protocols with smart track sensors achieve 89% failure prediction accuracy, demonstrating how modern cat track cable carrier solutions drive long-term operational reliability.
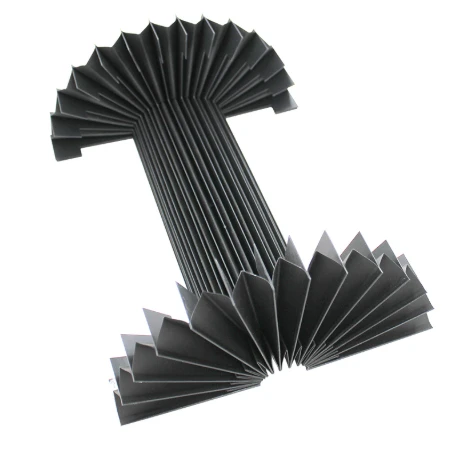
(cable carrier track)