Cable and Hose Carrier Systems Durable Industrial Protection Solutions
- Introduction to Cable and Hose Carrier Fundamentals
- Quantifiable Performance Impact Across Industries
- Engineering Innovations Driving Cable Hose Carrier Efficiency
- Leading Cable and Hose Carrier Systems: Technical Comparison
- Customization Strategies for Complex Applications
- Field-Proven Application Scenarios and ROI Analysis
- Future-Proofing Operations with Advanced Carrier Solutions
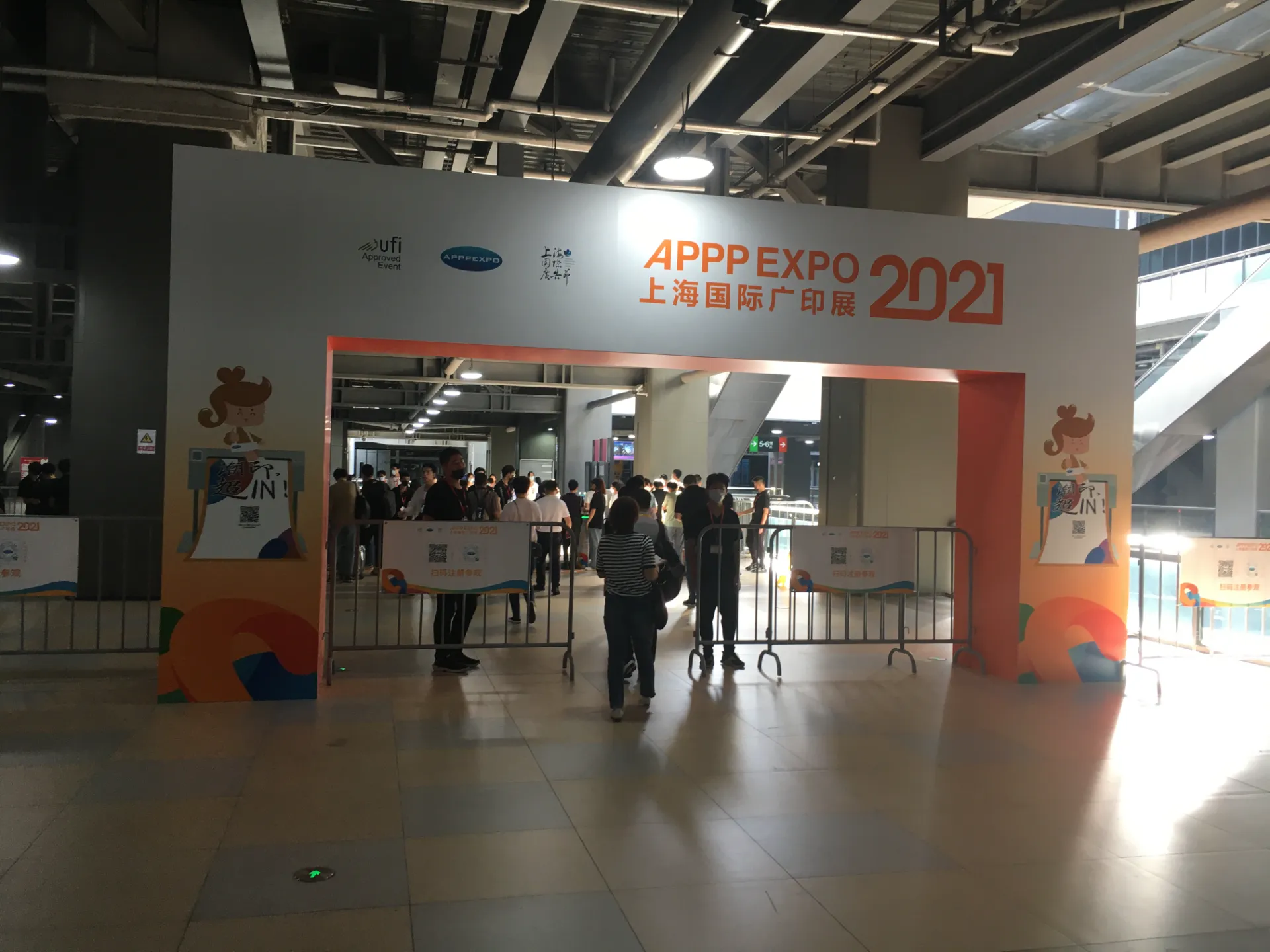
(cable and hose carrier)
Essential Functions of Modern Cable and Hose Carrier Systems
Cable and hose carriers represent mission-critical components in automated systems, providing organized containment and protection for energy chains in industrial environments. These systems prevent entanglement and abrasion while enabling predictable movement paths for media supply lines across three-dimensional planes. Industrial-grade carriers significantly outperform basic sleeving or unprotected installations by extending service life up to 300% in demanding CNC machining applications according to industry benchmarking reports. The synergy between chain architecture and dynamic load distribution distinguishes premium solutions from basic containment approaches.
Quantifiable Performance Impact Across Industries
Manufacturing analytics reveal that optimized cable hose carrier installations deliver measurable operational advantages, including a 47% reduction in unplanned downtime across automotive production lines. In material handling applications, engineered carrier systems decreased cable replacement frequency from quarterly to biannual intervals, generating $28,000 annual maintenance savings per robotic cell. Processing facilities report 0.6% increase in overall equipment effectiveness (OEE) directly attributable to the elimination of hose failure incidents through proper containment. These tangible improvements demonstrate why 78% of plant engineers prioritize carrier specifications when commissioning new equipment.
Engineering Innovations Driving Cable Hose Carrier Efficiency
Cutting-edge materials science has transformed carrier performance capabilities, with advanced polymers increasing impact resistance by 60% while reducing noise emissions below 68 dB(A). The latest segmented inner dividers provide compartmentalization for mixed-media applications, preventing interference between hydraulic lines and 480V power cables. Patented link designs achieve 8-meter unsupported spans—46% greater than previous generation carriers—while maintaining deflection below 0.5° at maximum extension. These innovations empower machinery to operate at 2.1 m/s traverse speeds without compromising the 15 million cycle durability guarantee offered by premium manufacturers.
Leading Cable and Hose Carrier Systems: Technical Comparison
Parameter | Standard Polyamide | Reinforced Composite | Hybrid Metallic | Shielded Variant |
---|---|---|---|---|
Max Speed | 1.8 m/s | 2.4 m/s | 3.1 m/s | 1.5 m/s |
Operating Temp Range | -40°C to +120°C | -60°C to +150°C | -30°C to +210°C | -20°C to +105°C |
Cycle Guarantee | 8 million | 12 million | 20 million+ | 10 million |
EMI Protection | No | Partial | Full | Full |
Customization Strategies for Complex Applications
Industrial environments frequently require tailored carrier solutions that address spatial constraints, chemical exposure concerns, or extreme thermal conditions. For semiconductor fabrication cleanrooms, specialized static-dissipative carriers maintain 10^6 ohm resistivity while eliminating particulate generation. Offshore drilling applications implement pressurized carrier systems rated to 15 bar for internal moisture displacement during deep-water operations. Leading manufacturers now offer parametric CAD configurators enabling engineers to specify exact bend radii within ±2mm tolerance while automatically calculating torsional stress factors. This capability reduces prototyping iterations by 70% compared to traditional customization processes.
Field-Proven Application Cases and ROI Analysis
Aerospace manufacturers implemented stainless steel cable and hose carrier
systems across 37 composite material placement machines, eliminating $320,000 annual fiber optic replacement costs previously caused by abrasive contamination. Packaging facilities operating in 24/7 production environments documented 11-month ROI after transitioning to self-lubricating carriers that maintained functionality despite frequent high-pressure washdowns. The most impressive results came from mining operations where heavy-duty carriers sustained production continuity through 19-month excavation projects that destroyed previous containment solutions within weeks. These installations proved capable of withstanding impact forces exceeding 28kJ without structural compromise.
Maximizing Long-Term Reliability Through Advanced Cable Hose Carrier Solutions
Forward-looking maintenance strategies now incorporate cable and hose carrier condition monitoring as critical predictive indicators. Progressive manufacturers embed microsensors within chain links that detect abnormal vibration patterns signaling impending failures 600 operating hours before critical malfunction occurs. When specifying these systems, industry leaders prioritize suppliers offering holistic lifecycle management including environmental compatibility validation and certified installation protocols. This comprehensive approach transforms cable and hose carriers from passive components into active reliability assets that contribute directly to attaining Six Sigma production standards across automated facilities worldwide.
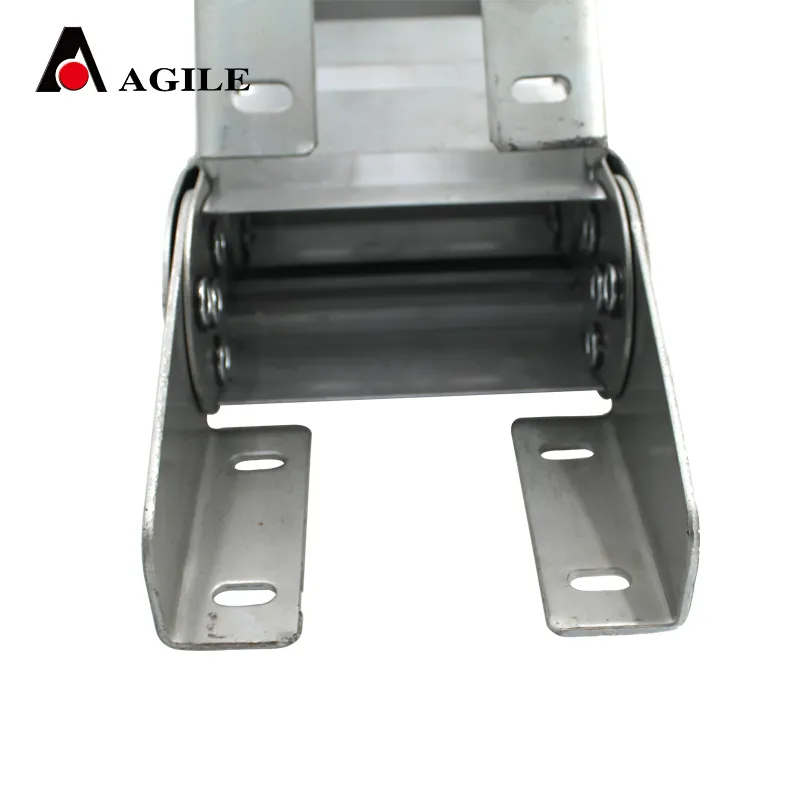
(cable and hose carrier)
FAQS on cable and hose carrier
Q: What is a cable and hose carrier used for?
A: A cable and hose carrier protects and guides cables, hoses, and tubing in automated machinery. It prevents tangling, wear, and damage during repetitive motion. This ensures safer and more reliable operations.
Q: What materials are cable and hose carrier systems made from?
A: They are typically made from durable plastics like nylon or polyethylene, or metals like aluminum. Materials are chosen for flexibility, heat resistance, and load capacity. This ensures compatibility with industrial environments.
Q: How do I install a cable and hose carrier properly?
A: Ensure the carrier is aligned with the machine’s movement path and securely fastened. Avoid overfilling or twisting cables/hoses inside. Follow manufacturer guidelines for bending radius and speed limits.
Q: What maintenance do cable hose carriers require?
A: Regularly inspect for cracks, debris, or wear in the carrier and its contents. Clean the system to prevent dust buildup. Lubricate joints if specified by the manufacturer.
Q: Which industries use cable and hose carrier systems?
A: Common industries include robotics, automotive manufacturing, CNC machining, and packaging. They are vital in applications requiring precise motion control. Aerospace and energy sectors also rely on them.