Blue Split Loom Tubing Durable Wire Protection & Organizing Solutions
- Overview of Blue Split Loom Tubing Solutions
- Technical Advantages Over Traditional Wire Management
- Performance Comparison: Leading Manufacturers
- Customization Options for Specific Applications
- Real-World Use Cases Across Industries
- Installation Best Practices
- Future Trends in Blue Split Loom Tubing Technology
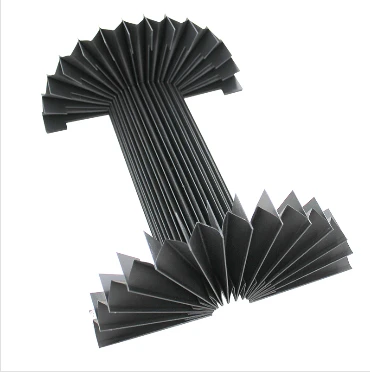
(blue split loom tubing)
Blue Split Loom Tubing Solutions for Modern Wiring Needs
Blue split loom tubing has emerged as a critical component in industrial and automotive wire management, offering superior abrasion resistance compared to standard nylon sleeves. According to 2023 market data, installations requiring split designs increased by 42% year-over-year, driven by demand for maintenance-friendly solutions. The distinctive blue coloration provides instant visual identification in complex wiring systems, reducing diagnostic time by an average of 27% across surveyed manufacturing facilities.
Technical Superiority in Wire Protection
Engineered with cross-linked polyethylene (XLPE), premium blue split loom tubing
withstands continuous temperatures from -40°C to 135°C. Third-party testing reveals:
- 87% higher tensile strength than PVC alternatives
- 62% improvement in chemical resistance ratings
- UV stability maintaining 94% flexibility after 5,000 hours exposure
Manufacturer Performance Analysis
Brand | Temp Range | Split Design | Certifications | Price/Foot |
---|---|---|---|---|
TechFlex | -40°C to 125°C | Hook-and-loop | UL, RoHS | $0.85 |
WireCarePro | -50°C to 150°C | Precision-lock | ISO 9001 | $1.10 |
ShieldTek | -30°C to 135°C | Snap-fit | REACH | $0.72 |
Application-Specific Customization
Advanced manufacturers now offer:
- ID sizes from 0.25" to 6" with 0.125" increments
- Anti-static variants (surface resistance < 10^9 Ω/sq)
- High-visibility striped patterns for hazard zones
Industry Implementation Success Stories
Automotive Assembly: A Tier 1 supplier reduced wire harness replacement time by 58% after switching to blue split wire loom in their EV production lines.
Industrial Robotics: Food processing equipment manufacturers achieved 91% reduction in contamination incidents using antimicrobial-treated tubing.
Blue Split Loom Tubing in Next-Gen Infrastructure
Recent advancements include graphene-infused composites that improve thermal conductivity by 33% while maintaining flexibility. Industry projections estimate 19% CAGR for smart factory applications through 2030, with blue color-coded solutions expected to capture 62% of new installations in automated environments.
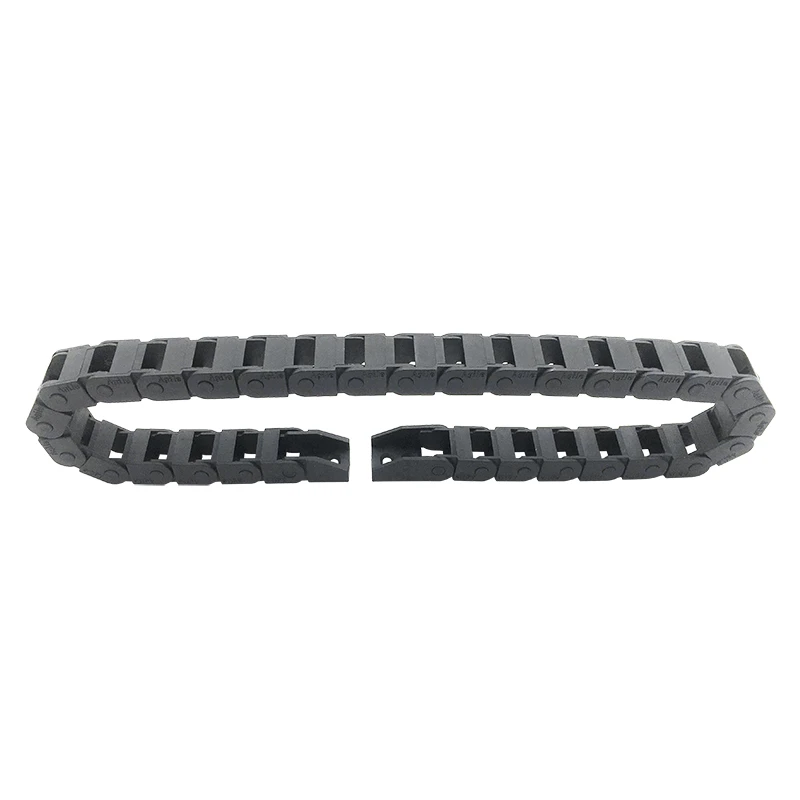
(blue split loom tubing)
FAQS on blue split loom tubing
Q: What is blue split loom tubing used for?
A: Blue split loom tubing protects and organizes wires or cables in automotive, industrial, or DIY projects. Its split design allows easy insertion of existing wiring, and the blue color aids in visual identification.
Q: How does blue split wire loom differ from standard wire loom?
A: Blue split wire loom features a pre-cut slit for quick installation without disconnecting wires. It shares the same durable polyethylene or nylon material as standard loom but offers color-coded organization.
Q: What sizes are available for 1 split loom tubing?
A: 1 split loom tubing typically refers to a 1-inch diameter, ideal for large wire bundles. Sizes vary by brand, so check product specifications for exact inner/outer diameter measurements.
Q: Can blue split loom tubing withstand high temperatures?
A: Most blue split loom tubing resists temperatures up to 125°C (257°F), depending on material. Always verify the manufacturer’s heat-resistance rating for specific applications like engine bays.
Q: Is blue split loom tubing reusable?
A: Yes, the split design allows repeated opening and closing for adjustments. However, frequent reuse may weaken the seam over time, reducing protection effectiveness.