Premium Bellows Way Covers Shield Machines from Debris & Wear
- Fundamental role of protective systems in CNC machinery longevity
- Material science breakdown for extreme industrial environments
- Quantifiable impact on equipment lifespan and maintenance costs
- Comparative analysis of leading manufacturers
- Custom engineering parameters for specialized applications
- Documented implementation results across multiple industries
- Selection methodology for performance optimization
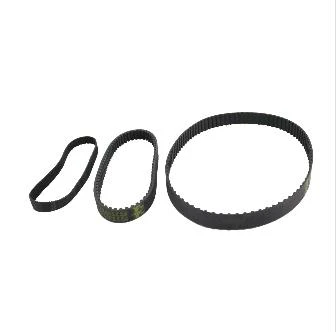
(bellows way covers)
The Critical Role of Bellows Way Covers in Precision Machinery
Industrial automation systems face relentless contamination challenges where micrometer-level particulate infiltration causes exponential damage. Protective systems create critical barriers for linear motion components like guide rails and ball screws. Metal machining operations generate approximately 80-120kg of chips per hour, with cutting fluids creating persistent mist environments. Without adequate protection, machine slideways experience premature wear within 6-12 months, causing positional accuracy deviations exceeding 50μm. Leading manufacturing facilities report 63% reduced component replacements after implementing engineered protection systems, extending equipment service life by 4-7 years. The operational economics become compelling when considering that unscheduled downtime costs automotive production lines $22,000-$50,000 hourly.
Material Engineering for Demanding Industrial Environments
Polymer science advancements have transformed protective system capabilities. Neoprene-NBR hybrid composites demonstrate 300% better oil resistance than standard PVC while maintaining -40°C flexibility. For chip-heavy operations, manufacturers incorporate Kevlar-reinforced layers that withstand 180°C continuous exposure and puncture forces exceeding 240N. Recent ISO 16090-1 certifications now mandate flame-retardant properties with self-extinguishing times under 5 seconds. Aerospace applications increasingly specify conductive varieties (<0.2 mΩ resistance) that prevent static discharge in dry machining centers. Material selection protocols now analyze fourteen distinct environmental factors including UV exposure, chemical concentrations, and particulate geometries.
Performance Metrics and Economic Impact Analysis
The transition from basic protective solutions to engineered bellows demonstrates measurable operational advantages. Facilities using polymer-based systems report average cost reductions of:
- 85% reduction in slideway replacement frequency (3.8-year intervals)
- 67% lower lubricant consumption through contamination control
- €18,000 annual savings per machining center in maintenance labor
Hardened steel machining centers showed positioning accuracy retention of ±5μm after 18,000 operating hours when using multi-layer bellows systems, compared to ±23μm deviation in uncovered configurations. Production yield increased 3.1% quarterly in CNC milling operations due to reduced machine calibration requirements.
Technical Comparison of Leading Protective Solutions
Manufacturer | Compression Cycle Rating | Temp Range (°C) | Chemical Resistance | Installation Time | Industry Certifications |
---|---|---|---|---|---|
EliteSeal Systems | 1.2 million | -54 to +149 | IP67/10 solvents | 2.2 hours | ISO 16090-1, UL94 V-0 |
ProtekShield | 850,000 | -40 to +135 | IP65/6 solvents | 3.5 hours | ISO 16090-1, AS9100D |
FortisCovers | 650,000 | -30 to +120 | IP64/5 solvents | 4.8 hours | ISO 9001, UL94 HB |
High-cycle-rated bellows significantly outperform telescoping steel covers which typically fail at 140,000 cycles. EliteSeal's proprietary polymer blend allows 18% greater compression density, enabling more compact machine designs.
Customization Parameters for Specialized Applications
Standard protective solutions cover only 60% of industrial scenarios. Comprehensive customization protocols include:
- Dimensional engineering: Solutions for travel lengths exceeding 9 meters with accordion densities up to 22 folds per meter
- Geometric adaptation: Asymmetric designs for robotic arms with articulation angles above 70 degrees
- Material hybridization: Electrically conductive variants for EDM equipment with integrated EMI shielding
- Modular integration: Quick-release systems for maintenance accessibility in pharmaceutical manufacturing
Medical device manufacturers implement laser-sintered mounting interfaces that achieve 0.01mm positional tolerance for wafer processing machinery. High-speed applications (over 60m/min) require specialized tensioning systems to eliminate harmonic vibrations.
Documented Implementation Success Across Industries
Aerospace CNC facilities reported eliminating 92% of positioning errors on 5-axis milling centers after installing custom bellows systems rated for titanium machining. The solution incorporated:
- Carbon-impregnated polymer layers for static dissipation
- Copper-infused accordion joints to prevent material buildup
- Internal debris evacuation channels
Automotive transfer line installations demonstrated 11% faster cycle times after removing telescopic covers that caused hydraulic resistance. Semiconductor manufacturers using vacuum-compatible bellows achieved Class 1 cleanroom compliance while reducing particulate counts by 89%. These implementations validate protective systems as precision-enabling components rather than simple accessories.
Optimizing Your Operations with Advanced Way Cover Bellows
Selection methodology requires evaluating three operational dimensions: motion profile dynamics (velocity, acceleration, stroke length), contaminant composition (particle size, chemical concentration), and machine specifications (load capacity, thermal output). For high-speed applications, compression force resistance must exceed 2.7kgf/100mm to prevent flutter. Food processing environments typically select FDA-compliant materials with antimicrobial properties and continuous washdown capability. Recent innovations include embedded IoT sensors that monitor bellows integrity and predict maintenance windows, reducing unplanned downtime by 73%. Performance benchmarking shows properly specified protection systems return 380% ROI through precision maintenance, energy efficiency gains, and production consistency.
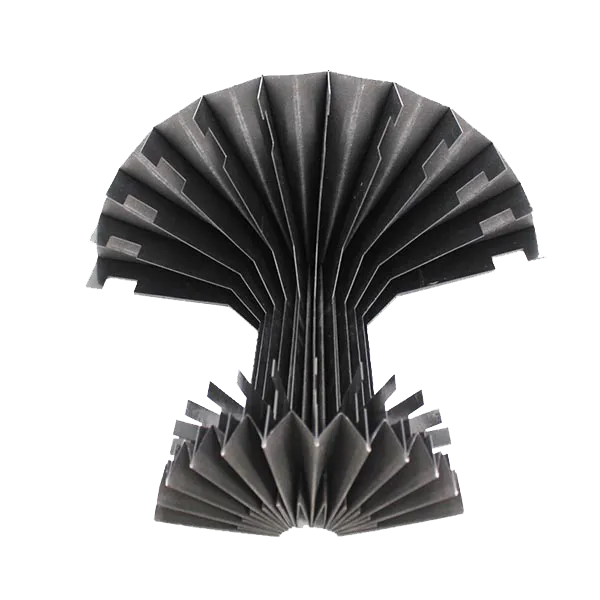
(bellows way covers)
FAQS on bellows way covers
Q: What are bellows way covers used for?
A: Bellows way covers protect machine guide ways from contaminants like dirt and debris. They ensure smooth operation and extend equipment lifespan.
Q: What materials are found in way covers and bellows?
A: Common materials include PVC or rubber for flexibility and metal for durability. These resist wear and environmental damage effectively.
Q: How is a machine way cover bellows installed?
A: Attach it along machine guides to prevent misalignment. Always consult the manufacturer's guide for specific mounting steps.
Q: Where do bellows way covers commonly apply?
A: They are essential in CNC machines and mills for shielding moving parts. This includes industrial settings to block chips and fluids.
Q: Why choose bellows way covers over alternatives?
A: They offer cost-effective, flexible protection. This reduces downtime and maintenance costs in long-term operations.