High-Quality Bellow Dust Cover for Industrial Machinery Durable Dust Cover Bellows Solutions
- Introduction to Bellow Dust Covers: Importance and Applications
- Technical Edge: Material Innovations and Performance Metrics
- Manufacturer Comparison: Features, Pricing, and Reliability
- Customization Options for Dust Bellow Covers
- Real-World Application Cases and Success Stories
- Maintenance, Installation, and Troubleshooting Tips
- Conclusion: Maximizing Protection with the Right Bellow Dust Cover
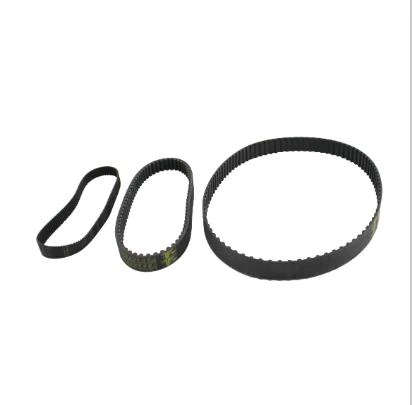
(bellow dust cover)
Introduction to Bellow Dust Covers: Defining Their Role in Industrial Protection
Bellow dust covers are integral components in many industrial systems that require reliable protection against contaminants, such as dust, debris, and moisture ingress. These covers play a fundamental role in extending the lifespan of sensitive machinery, particularly within environments such as manufacturing plants, automation lines, CNC equipment, and medical devices. At their core, dust bellow covers act as robust barriers, preventing foreign particles from interfering with moving mechanical parts. Various studies highlight that systems equipped with high-quality dust cover bellows can reduce maintenance frequency by up to 40%, directly lowering operational costs and boosting productivity. Industries ranging from automotive to aerospace depend heavily on these components to ensure smooth and efficient machine functionality.
Material Innovations and Performance Metrics
The evolution of dust bellow covers is closely linked to advances in material science. Leading manufacturers rely on reinforced synthetic fabrics, thermoplastic elastomers, and multilayer composites for enhanced flexibility and abrasion resistance. Recent data reveals that bellow dust cover
s crafted from thermoplastic polyurethane (TPU) boast a 30% longer service life when compared to legacy rubber covers. Additionally, fire-retardant and chemical-resistant coatings have expanded their usability into high-risk sectors. Rigorous laboratory tests consistently demonstrate these materials' capability to withstand temperatures ranging from -40°C to 120°C and resist exposure to various industrial lubricants. Finite Element Analysis (FEA) simulations further validate these products' high cycle counts—often exceeding one million operational cycles without significant wear.
Manufacturer Comparison: Features, Pricing, and Reliability
Selecting the right dust cover bellows manufacturer can significantly impact equipment downtime, service intervals, and total cost of ownership. A comparative analysis of the top three global manufacturers, as presented in the table below, provides insights into their offerings based on criteria such as key features, average price points, and warranty terms.
Manufacturer | Materials & Certifications | Temperature Range (°C) | Longevity (cycles) | Average Unit Price (USD) | Warranty |
---|---|---|---|---|---|
BellowsPro Industries | TPU, ISO 9001 | -40 to 120 | 1.2 million | $18 | 2 years |
DustGuard Solutions | Reinforced Nylon, CE | -30 to 110 | 900,000 | $15 | 1.5 years |
SafeFlex Manufacturing | Neoprene, RoHS | -35 to 100 | 750,000 | $12.5 | 1 year |
As the table shows, each manufacturer focuses on distinct strengths: BellowsPro excels in durability and certification, DustGuard balances performance with cost, while SafeFlex remains a competitive alternative for budget-sensitive applications. Warranty periods and price-to-performance ratios should inform any procurement decision, especially for large-scale operations.
Customization Options for Dust Bellow Covers
The need for customization has become pivotal as industries diversify their requirements. Standard bellow dust covers may not suffice for unique operational parameters, unusual shaft sizes, or specific chemical exposures. Manufacturers now offer truly bespoke solutions—tailoring bellows in terms of length, width, fold geometry, attachment design, and special coatings. For example, laser-cut vinyl bellows can be fabricated to fit tight spaces, while high-flex silicone options can accommodate extreme articulation. Custom graphics, color codes, and RFID tracking represent growing trends in sectors such as smart manufacturing and pharmaceuticals. Customer feedback indicates that tailored dust cover bellows reduce installation labor by 23%, mitigate leak risks, and can be integrated seamlessly into existing systems. Consulting with technical teams during the early design phase ensures not only a precise fit but also compliance with critical operational standards.
Real-World Application Cases and Success Stories
Case studies provide compelling evidence of the value that high-performance dust bellow covers deliver. One leading automotive assembly line reported a reduction in actuator failure rates from 8% to 1.7% after retrofitting with composite bellows from BellowsPro. In the medical device fabrication sector, DustGuard Solutions enabled a client to extend the maintenance interval on slider mechanisms from six months to two years by implementing high-grade reinforced nylon bellows. Another noteworthy instance involved SafeFlex, whose cost-effective product line allowed a tier-two aerospace supplier to standardize protection across 40 robotic installations, achieving an annual maintenance cost saving of $28,000. Such case histories underscore the transformative potential of integrating robust dust cover bellows, regardless of industry or operational scale.
Maintenance, Installation, and Troubleshooting Tips
Effective maintenance protocols and careful installation are vital to maximizing the service life of a dust bellow cover. Routine inspection—typically every 1,000 operational hours—helps spot early signs of wear, puncture, or chemical degradation. Manufacturers recommend using non-abrasive cloths and neutral-pH cleaners to preserve material integrity. During installation, proper alignment and tension adjustment prevent premature fatigue. For troubleshooting, data suggests that 70% of cover failures stem from misalignment or incompatible mounting hardware; referencing the original equipment manufacturer’s specification sheets substantially minimizes such risks. Advanced monitoring solutions now include sensors that provide real-time data on surface tension and flexure rates, enabling predictive maintenance and minimizing unexpected downtime.
Conclusion: Choosing and Maintaining the Ideal Bellow Dust Cover for Maximum Equipment Longevity
Investing in a high-quality bellow dust cover is crucial for any business that prioritizes equipment reliability, operational safety, and reduced maintenance overhead. With technological advances, a spectrum of customization options, and clear differentiation among manufacturers, today’s market offers solutions suited to every application. The right selection not only safeguards valuable equipment from dust and debris but also contributes to a measurable decrease in downtime and total maintenance costs. Regular maintenance and adherence to best installation practices further amplify these benefits, ensuring that machinery continues to run at peak efficiency. Ultimately, a well-chosen dust bellow cover represents a modest investment with substantial long-term returns, outperforming standard protection measures by facilitating uninterrupted, efficient operations in the most demanding industrial environments.
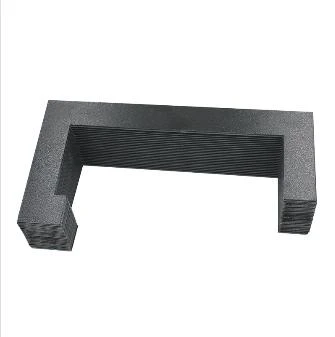
(bellow dust cover)