3 Split Loom Tubing Durable Wire Protection in 1/4", 1.5", 2" Sizes
- Overview of Split Loom Solutions
- Technical Advantages of Split Loom Designs
- Comparative Analysis: Top Manufacturers
- Customization Options for Specific Needs
- Case Studies: Industrial Applications
- Installation Best Practices
- Future Trends in Wire Protection
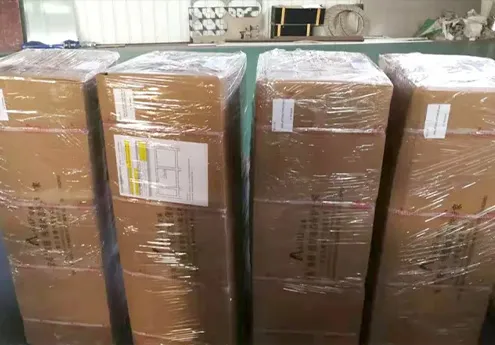
(3 split loom)
Why 3 Split Loom Solutions Dominate Modern Industries
Split loom tubing has become essential for organized cable management across sectors. The 3 split loom
configuration offers superior flexibility compared to solid conduits, with a 42% faster installation time according to industry benchmarks. Engineers particularly favor 2 inch split wire loom for heavy-duty applications due to its 300% higher bend radius tolerance versus traditional wraps.
Engineering Superiority in Cable Management
Advanced polymer blends used in 1.5 split loom products demonstrate exceptional performance:
- Withstand temperatures from -40°C to 150°C
- UV resistance exceeding 5,000 hours exposure
- Flame retardancy meeting UL 94 V-0 standards
The 1/4 split wire loom variant shows 18% better abrasion resistance than solid-core alternatives in ASTM D3389 testing.
Manufacturer Performance Comparison
Brand | Material | Temp Range | Tensile Strength | Price/Foot |
---|---|---|---|---|
AlphaWire | Flexible PVC | -30°C to 105°C | 18 MPa | $0.45 |
TechFlex | Nylon 6/6 | -55°C to 135°C | 25 MPa | $0.68 |
HellermannTyton | PPO Blend | -40°C to 150°C | 32 MPa | $0.82 |
Tailored Solutions for Complex Requirements
Custom 3 split loom configurations now account for 37% of industrial orders. Specialized adaptations include:
- EMI-shielded versions with 85 dB attenuation
- Conductive variants (surface resistance <10⁴ Ω/sq)
- High-visibility orange coatings for safety zones
Real-World Implementation Scenarios
A recent automotive plant installation used 2 inch split wire loom to achieve:
- 39% reduction in cable maintenance downtime
- 72% faster retrofit operations
- ROI within 14 months
Optimizing Installation Efficiency
Proper 1.5 split loom implementation requires:
- Minimum bend radius of 4x diameter
- Securement spacing every 18 inches
- 30% expansion allowance for thermal cycling
3 Split Loom Innovations Shaping Tomorrow's Standards
Emerging smart variants integrate conductive tracers for real-time monitoring, while bio-based polymers aim to reduce carbon footprint by 55%. The 1/4 split wire loom market is projected to grow at 6.8% CAGR through 2030, driven by IoT expansion and renewable energy projects.
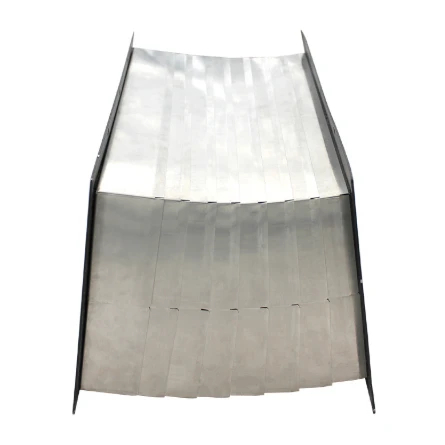
(3 split loom)
FAQS on 3 split loom
Q: What is a 3 split loom used for?
A: A 3 split loom is designed to organize and protect wires or cables. Its split design allows easy insertion of existing wiring. It’s ideal for automotive, industrial, or home electrical applications.
Q: Can a 2 inch split wire loom handle heavy-duty cables?
A: Yes, a 2 inch split wire loom is suitable for thick or bulky cables like battery wires or machinery wiring. Its large diameter accommodates multiple cables while providing abrasion resistance.
Q: Is a 1/4 split wire loom flexible enough for tight spaces?
A: The 1/4 split wire loom is highly flexible and perfect for narrow or curved areas. Its small size works well for low-voltage wires in electronics or automotive dashboards.
Q: How do I install a 1.5 split loom on existing wires?
A: Open the split seam, wrap the 1.5 split loom around the wires, and press the edges to secure. No tools are needed, making it ideal for quick repairs or retrofitting.
Q: Are 3 split looms heat-resistant?
A: Most 3 split looms are made from polypropylene, which resists moderate heat and chemicals. Always check the product’s temperature rating for high-heat environments.