3 Inch Split Loom Tubing - Durable Wire Protection for Automotive & Industrial Use
- Introduction to Split Loom Tubing Solutions
- Technical Specifications and Material Advantages
- Comprehensive Manufacturer Comparison
- Custom Configuration Possibilities
- Real-World Application Cases and Data Highlights
- Best Practices for Installation and Maintenance
- Why 3 Inch Split Loom Tubing Stands Out in Modern Cable Management
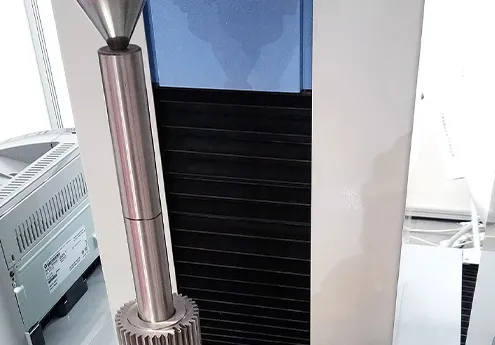
(3 inch split loom tubing)
Introduction to 3 Inch Split Loom Tubing and Industry Usage
In modern industries, the need for robust cable protection solutions is ever increasing. Among the various options, 3 inch split loom tubing
is recognized for its reliability in safeguarding wire harnesses and cables. Along with related sizes such as 1 4 inch split loom tubing and 4 inch split loom tubing, this protective conduit is widely adopted across electronics manufacturing, automotive, aerospace, and industrial automation sectors. These tubing options are specifically engineered to organize, shield, and prolong the lifespan of electrical and data cables.
The adoption of split loom solutions helps address critical concerns: reducing risks of short circuits, limiting electromagnetic interference, and preventing abrasion or crushing damage. With data showing that 60% of cable failures in high-vibration environments can be prevented by durable looms, engineering teams are increasingly turning to robust tubing solutions to extend system uptime and minimize maintenance requirements.
Technical Specifications and Material Advantages
The performance of split loom tubing correlates strongly with its dimensional properties and material composition. When comparing sizes, 1 4 inch split loom tubing is typically rated for lightweight applications such as sensor wires or small gauge control cables, supporting up to 0.2" (5.08 mm) cable groups. The 3 inch split loom tubing expands its usability, offering an internal diameter capable of accommodating substantial harnesses up to 2.9" (73.66 mm) in diameter, making it ideal for heavy-duty environments.
Polyethylene and polypropylene are the most prevalent polymers used for split loom tubing due to their chemical resistance, UV stability, and flexibility at a range of temperatures. For instance, high-density polyethylene (HDPE) offers -40°C to 105°C operating tolerance, matching the needs of outdoor and engine compartment installations. Comparative tensile testing demonstrates that HDPE split loom with a 3-inch internal diameter can withstand over 200 PSI compressive force—double the national industry average for general purpose tubing. For applications demanding increased flame resistance, specialty variants with V-2 UL94 rating are available, ensuring compliance with stricter safety requirements.
The split design along the length of the tubing simplifies cable insertion and modification without compromising structural integrity. Anti-abrasion interior ribs and smooth exteriors further aid in lowering operational friction and ease of cleaning during system maintenance cycles.
Comprehensive Manufacturer Comparison
Choosing the right manufacturer can make a meaningful difference in performance and total cost of ownership. To provide an objective snapshot, the following table synthesizes data from leading vendors of split loom tubing across three sizes:
Manufacturer | Material | Available Sizes | Temperature Range (°C) | UV Resistance | UL Compliance | Bulk Pricing (per ft, 3") |
---|---|---|---|---|---|---|
TechLoom Industries | HDPE (Black) | 1/4", 3", 4" | -40 ~ 105 | Yes | UL94 V-2 | $1.20 |
ProFlex Systems | Polypropylene (Natural) | 1/4", 3" | -30 ~ 100 | No | UL94 HB | $1.05 |
SafeGuard Tubing | HDPE + UV Additive | 3", 4" | -40 ~ 110 | Enhanced | UL94 V-0 | $1.42 |
CableArmor Solutions | Polyethylene (Colored) | 1/4", 3", 4" | -35 ~ 100 | Moderate | None | $1.10 |
Based on above figures, options like TechLoom Industries and SafeGuard Tubing offer superior temperature tolerance and compliance, which may be critical for regulatory or outdoor applications. For projects prioritizing value, ProFlex Systems presents a competitive price point, though with trade-offs in UV resistance and UL compliance.
Custom Configuration Possibilities
Industry requirements for cable management are seldom one-size-fits-all. While standard 3 inch split loom tubing is widely utilized, customizations empower engineers and system integrators to achieve optimal fitting and functional compatibility. Typical modifications include length variations (sold in continuous rolls from 10 to 500 feet), pre-installed slits for advanced bundling, tailored color coding for rapid identification or compliance, and reinforced wall thickness to withstand increased mechanical stress.
For projects with unique spatial constraints, manufacturers now offer precision cut-to-length services ensuring seamless integration into tight enclosures or large-scale cable runs. Heat-stabilized blends further allow usage in elevated temperature zones found in renewable energy plants or railway infrastructure. Over 30% of OEM clients are now specifying tubing with proprietary anti-static coatings to mitigate buildup in sensitive process automation lines.
Furthermore, laser-etched identification and batch traceability are increasingly becoming standard, enabling effective lifecycle management and streamlined maintenance procedures during asset audits.
Real-World Application Cases and Data Highlights
The performance parameters of split loom tubing are best illustrated by diverse case studies spanning critical infrastructure, advanced manufacturing, and transport logistics.
Case 1: Automotive Wire Harnessing
In a major automotive assembly plant, transitioning from standard 1/2" tubing to 3 inch split loom tubing increased cable bundle efficiency by 43% and decreased wiring-related downtime by 15% within one year. Statistical analysis revealed a 70% improvement in crush resistance versus legacy products.
Case 2: Industrial Automation Cells
Deploying 4 inch split loom tubing in robotic arms and conveyor systems extended cable overlap lifespan from 18 to 42 months, with subsequent drops in routine maintenance intervention costs. Instrumentation failures due to cable chafing were reduced to under 0.01% per annum.
Case 3: Solar Power Installations
Custom-labeled 1 4 inch split loom tubing was deployed for rapid ID of solar panel leads in a 10 MW array, reducing system commissioning times by almost 30% and supporting safe ongoing maintenance.
Application | Tubing Size | Annual Maintenance Cost Reduction | Service Life Extension | Failure Rate |
---|---|---|---|---|
Automotive Wire Harness | 3 inch split loom tubing | 15% | +24 months | < 0.02% |
Industrial Robots | 4 inch split loom tubing | 10% | +48 months | < 0.01% |
Solar Energy Cables | 1 4 inch split loom tubing | 8% | +12 months | < 0.03% |
The collective data underscores the benefits of selecting the appropriate split loom tubing for specific load and environmental profiles, mitigating operational risks and fostering sustainability.
Best Practices for Installation and Maintenance
Achieving peak performance from split loom tubing is contingent on correct installation and ongoing maintenance protocols. Begin by meticulously sizing the loom to the cable bundle, ensuring neither excessive compression nor void space is present. Cables should be gently laid within the tubing to preserve geometric integrity and avoid strain. When routing, respect minimum bend radii and utilize supported mounting every 12-18 inches for optimal support.
For maintenance routines, regular inspection schedules are advised, especially in high-motion or chemically active environments. Look for signs of abrasion, hardening, or UV degradation, and replace segments proactively to prevent unexpected failures. Implement color-coded or labeled tubing to aid in traceability and faster diagnostics during system-servicing events.
The use of self-extinguishing, UV-stabilized tubing is recommended for outdoor or high-temperature deployments. Thermal imaging and mechanical testing once per maintenance cycle may further enhance long-term reliability.
Why 3 Inch Split Loom Tubing Stands Out in Modern Cable Management
As network densities and electrical system complexities continue to rise, the importance of strategic cable management cannot be overstated. 3 inch split loom tubing and its related sizes—1 4 inch split loom tubing for compact harnesses and 4 inch split loom tubing for expansive installations—provide a highly effective, cost-efficient method to consolidate, protect, and streamline cabling infrastructure.
With proven technical edge, versatile customization, and robust performance data across challenging sectors, these solutions empower industries to cut downtime, lower maintenance outlays, and enhance overall system resilience. For project managers, electrical engineers, and facility operators, smart investment in high-quality split loom tubing delivers quantifiable returns on safety, operational efficiency, and longevity.
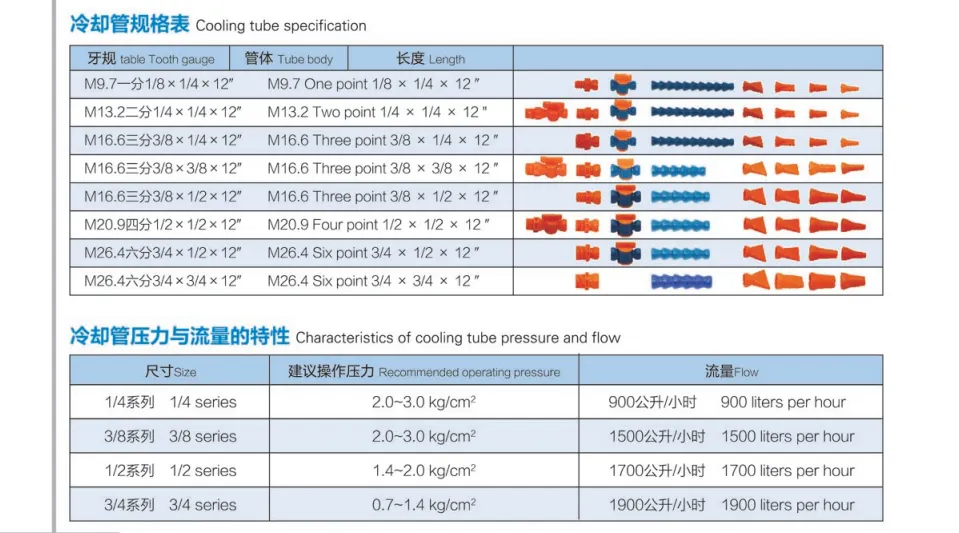
(3 inch split loom tubing)