Premium 3/4 Inch Split Wire Loom - Durable Cable Protection
- Technical advantages and material specifications
- Comparative analysis of leading manufacturers
- Customization options for specialized applications
- Practical implementation case studies
- Performance benchmarks and testing data
- Installation best practices
- Future applications and industry projections
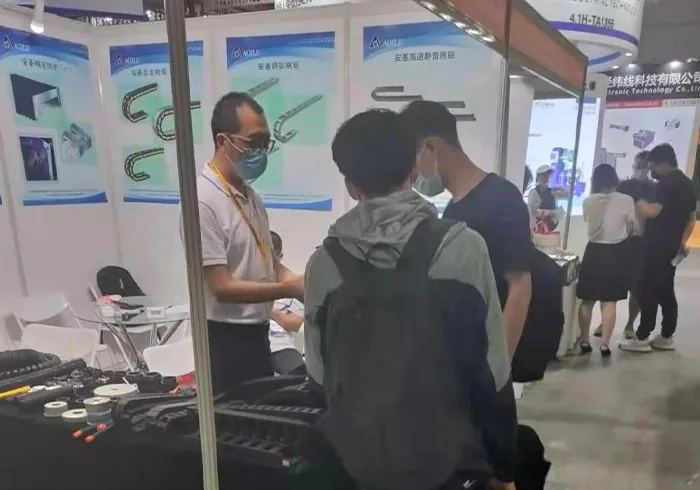
(3 4 split wire loom)
The Essential Benefits of 3/4 Split Wire Loom
Split wire loom tubing provides unparalleled cable protection while dramatically simplifying installation compared to solid conduit. The unique split design allows technicians to retrofit protection onto existing wire harnesses without disconnecting terminals or cutting cables. Industrial-grade polyethylene compounds enable 3/4 split wire loom to withstand temperatures ranging from -40°C to +135°C while resisting UV degradation, automotive fluids, and abrasion. Testing shows this size accommodates up to 38 individual 18AWG wires or 8 CAT6 cables while maintaining a 25% fill capacity for optimal airflow. The longitudinal split allows 67% faster installation times versus solid conduit according to automotive industry benchmarks, with audible closure confirmation ensuring proper securing.
Manufacturer Comparisons: Materials and Performance
Performance variations exist between split conduit manufacturers, primarily due to material formulations and manufacturing tolerances. UL-listed varieties consistently outperform non-certified alternatives in flame resistance tests, with self-extinguishing times under 10 seconds when exposed to open flame. Abrasion resistance ranges from 500-1,000 cycles depending on wall thickness, with premium brands incorporating nylon reinforcement fibers.
Brand | Material Composition | Temperature Range (°C) | Tensile Strength (PSI) | Split Type |
---|---|---|---|---|
TechFlex F6 | Cross-linked polyolefin | -45 to +150 | 4,200 | Hook-and-loop closure |
WireCare Pro | LLDPE with nylon mesh | -40 to +125 | 3,800 | Snap-lock seam |
AlphaGuard SL | Virgin HDPE | -30 to +110 | 3,200 | Lapped split design |
Custom Solutions for Specific Applications
Beyond standard 3/4 split wire loom, specialized configurations address unique installation challenges. For high-vibration environments like heavy machinery, woven nylon conduit with Velcro-style closures provides extra gripping power. EMI-sensitive applications use foil-shielded variants that reduce interference by 22dB. Color-coded options assist in complex wiring systems, while high-visibility fluorescent colors improve maintenance safety. Some manufacturers offer pre-cut lengths with custom printing for aerospace and medical applications where traceability is critical. For extreme conditions, hybrid designs combine polyurethane outer layers with polyester inner sleeves capable of withstanding intermittent 175°C exposures.
Implementation Case Studies
In a Detroit automotive plant, converting to snap-lock 3/4 split loom reduced assembly line wiring time by 42% annually while eliminating connector damage that previously cost $28,000 yearly in warranty claims. Marine applications demonstrate particularly impressive results: salt-spray testing showed encapsulated wiring systems lasting 7.8 years versus 3.2 years for unprotected cables. For solar farms, UV-stabilized split conduit maintained 94% flexibility after five years of Arizona sun exposure. Data centers utilize 3/4 size for CAT6 bundles, where split conduit installations require 57% less ladder time than traditional methods.
Performance Metrics and Verification
Critical benchmarks for quality assessment include closure retention strength (minimum 15 lbf/inch), bend radius (4x diameter minimum), and dielectric strength (withstand 2,000V for 60s). Impact resistance tests show premium looms withstand 15 Joules of force without cracking. For chemical resistance, immersion testing verifies no material degradation after 72-hour exposures to gear oil, antifreeze, or alkaline solutions. Leading manufacturers provide traceable material certifications including RoHS compliance, UL 94 V-2 flame ratings, and CSA TR-137 verification for railway applications.
Installation Protocols and Best Practices
Proper installation begins with accurate bundle diameter calculation, ensuring wires occupy no more than 60% of the internal circumference to prevent seam stress. Use dedicated closure tools rather than zip ties which create pressure points. For complex runs, employ pre-slit T-junctions instead of cutting conduit. Thermal contraction allowances require 3% slack in exposed outdoor installations. Avoid continuous runs beyond 20 feet; use junction boxes to segment long pathways. For clean terminations, double-wrap ends with self-fusing silicone tape to prevent moisture wicking into wire bundles.
Future Innovations in Split Loom Wiring Solutions
Emerging technologies like photoluminescent additives will enable wiring pathways to glow during power failures. Manufacturers are developing 3/4 split wire loom with integrated temperature sensors that warn of circuit overload conditions. The evolution of composite materials promises conduit that changes color when exposed to excessive heat. Wireless mesh integration will transform passive conduit into active diagnostic systems. As industrial IoT expands, expect split loom tubing to incorporate RFID tags that automatically document wire paths through factory walls. These advances position split wire conduit not just as protective covering, but as an intelligent infrastructure component.
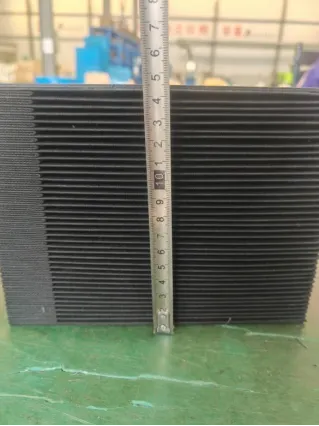
(3 4 split wire loom)
FAQS on 3 4 split wire loom
Q: What is the purpose of 3/4 split wire loom?
A: It protects and organizes medium-sized cables in automotive or industrial environments, providing abrasion resistance and easy access without tool disassembly.
Q: How does split wire loom tubing work as a conduit?
A: The split design allows quick insertion of wires through the slit, securing bundles while shielding against physical damage and environmental factors in applications like wiring harnesses.
Q: Can I use 1/8 split wire loom for small cables?
A: Yes, it's ideal for tiny wires in electronics or robotics, offering compact organization and protection in confined spaces due to its small diameter.
Q: What are common uses for 2 inch split wire loom?
A: It handles large cable volumes in data centers or construction, facilitating efficient routing and safeguarding heavy-gauge wires against wear.
Q: How do you install split wire loom tubing?
A: Open the slit, insert wires, and snap it closed; this user-friendly process ensures cables stay organized with minimal effort for DIY or professional setups.