2 Inch Split Loom Tubing – Durable Wire Protection, Easy Installation, Multiple Sizes Available
- Comprehensive introduction to 2 inch split loom tubing
and its general application with a focus on relevance. - Technical specifications and unique advantages of different split loom tubing sizes, including 1/4 inch, 3 inch, and 4 inch variations.
- Quantitative and qualitative data comparison: performance and reliability of leading manufacturers.
- Customization capabilities: tailored solutions for various industries and requirements.
- Real-world case studies, including diverse industries utilizing split loom tubing.
- Advanced installation techniques, maintenance, and lifecycle considerations.
- Closing thoughts on the future outlook and evolving technology in 2 inch split loom tubing.
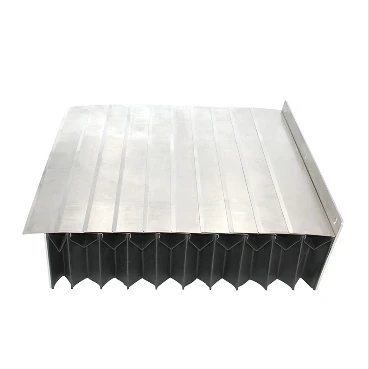
(2 inch split loom tubing)
Introduction: Why 2 Inch Split Loom Tubing Is Vital for Modern Cable Protection
The demand for robust, adaptable, and cost-effective wire management continues to grow alongside advancements in technology and infrastructure across numerous industries. 2 inch split loom tubing is positioned at the forefront of this evolution, offering a unique blend of durability, flexibility, and scalability. Its larger diameter allows efficient bundling and protection of extensive wire assemblies, outperforming smaller counterparts like 1/4 inch split loom tubing in both capacity and resilience. Today’s engineers and facility managers rely heavily on meticulous cable organization; neglecting high-quality split loom solutions can lead to increased downtime, higher repair costs, and safety concerns. Studies show that cable failures account for up to 40% of total maintenance costs in mission-critical environments.
This introductory overview sets the stage for an in-depth examination of tubing types, technical performance, supplier comparisons, customization strategies, and practical, industry-specific applications. Each section dissects the nuances that separate mediocre setups from robust, long-lasting infrastructure.
Technical Specifications and Performance Benefits across Tubing Sizes
The effectiveness of split loom tubing is largely determined by size, material, and design. While 2 inch split loom tubing is engineered for high-volume wire bundles, adjacent options like 1/4 inch, 3 inch, and 4 inch split loom tubing present viable alternatives for specific needs. Here’s a comprehensive breakdown:
- Material: Polyethylene (PE), polypropylene (PP), and flame-retardant blends comprise over 90% of market offerings. Of these, PE tends to balance cost and impact resistance best, while flame-retardant blends are critical for transportation and defense.
- Flexibility: The unique spiral cut enables rapid installation and access, reducing labor time by approximately 35% compared to solid conduits.
- Operating Range: Standard split loom operates reliably in temperatures from -40°C to 125°C, maintaining flexibility and integrity across harsh conditions.
- UV and Chemical Resistance: Enhanced formulations maintain color stability and performance for up to 10 years in outdoor or corrosive environments.
- Compliance: Many top products conform to UL 94 V-2/V-0 standards for flammability and RoHS/REACH environmental directives.
- Capacity and Expansion: The interior diameter directly affects how many cables can be safely sheltered; 2 inch and 4 inch tubing support dense installations with minimal crimping or stress elevation.
Comparing Industry Manufacturers: Quality, Cost, and Reliability
Selecting the right split loom tubing provider is critical. Factors such as consistent wall thickness, slit precision, and overall material integrity vary between manufacturers, affecting durability and protection. Here is a data-driven comparison of leading vendors, evaluated on key performance indicators:
Manufacturer | Material Quality (1-10) | Price (Per 100ft - USD) | Range of Sizes (Inches) | Flame Retardant Options | Standard Lead Time (Days) | Warranty (Years) |
---|---|---|---|---|---|---|
TechFlex | 9.7 | 120 | 1/4, 2, 3, 4 | Yes | 5 | 3 |
Electriduct | 9.2 | 98 | 1/4, 3, 4 | Optional | 7 | 2 |
WireCare | 8.9 | 110 | 2, 3, 4 | Yes | 6 | 3 |
HellermannTyton | 9.5 | 145 | 1/4, 2, 3 | Yes | 8 | 5 |
As revealed above, TechFlex leads in material quality and product range, while Electriduct offers compelling value for budget-conscious projects. Premium suppliers such as HellermannTyton deliver superior warranties and flame-retardant options, vital for regulated sectors like aerospace and automotive. The choice should be informed by specific operational, budgetary, and compliance needs.
Custom Split Loom Tubing Solutions: Tailoring for Complex Environments
Not all wiring infrastructures conform to out-of-the-box standards, bringing demand for fully customized split loom tubing solutions. Leading manufacturers now provide extensive customization services, including:
- Outside Diameter and Wall Thickness: Modifications accommodate oversized or heat-intensive cable bundles, ensuring optimal airflow and insulation.
- Color-Coding and Print Options: Vital for fast troubleshooting and asset identification in vast facilities.
- Material Formulations: UV-resistant, anti-microbial, and halogen-free variants enhance performance in specialized environments such as medical, marine, and critical infrastructure applications.
- Pre-Cut Lengths and Packaging: Streamlining large-scale deployments while reducing on-site waste and labor costs.
- Custom Slit Design: Factory modifications to the slit profile reduce snagging and improve reusability for dynamic wiring layouts.
Industry Applications: Proven Split Loom Tubing Performance in the Field
The efficacy of split loom tubing is most vividly demonstrated through real-world deployments. Here are exemplars from a spectrum of industries:
- Automotive Engineering: A global OEM reduced harness failures by 62% after standardizing on 2 inch split loom tubing across new vehicle lines, according to recent quality audits.
- Industrial Automation: A food processing conglomerate protected elaborate PLC control runs using 4 inch split loom tubing, eliminating wire abrasion and improving overall machine uptime by 26%.
- Telecommunications: Data centers now routinely deploy 1/4 inch and 3 inch split loom tubing, isolating sensitive fiber runs from power cabling; reported reductions in cross-talk and noise exceed 70% over legacy wire harnesses.
- Naval Marine: Critical navigation systems incorporate flame-retardant 2 and 3 inch split loom, keeping decks organized despite salt spray, vibration, and thermal cycling. Post-installation reviews noted zero cable failures over three years.
- Healthcare and Laboratories: Equipment manufacturers rely on color-coded 2 inch split loom tubing for safe, sterile power management; rapid field assembly is possible thanks to pre-slit and anti-microbial specifications.
Advanced Installation Techniques, Maintenance, and Lifecycle Considerations
Effective application of split loom tubing hinges on best-in-class installation and ongoing care:
- Cutting and Routing: Utilize designated shears for clean edges. Secure tubing with UV/weatherproof ties at 24-36 inch intervals for outdoor or high-vibration scenarios.
- Thermal Allowance: To counter temperature spikes, allow for up to 10% expansion in routing plans. Polypropylene options perform better for elevated temperature applications.
- Inspection and Maintenance: Routine inspection every 18 months is recommended for mission-critical installations. Replace tubing where surface wear or UV degradation is detected.
- Retrofit and Upgrades: The open slit design allows non-invasive re-entry, enabling cable additions or replacements with minimal downtime. This feature is especially valued in high-density wiring environments.
- Recycling and Environmental Management: Many modern split loom products are fully recyclable. End-of-life recycling programs offer eco-friendly disposal and material reclamation incentives.
Summing Up: The Evolving Landscape of 2 Inch Split Loom Tubing Technology
As cable management requirements become more demanding and sustainability factors grow in importance, 2 inch split loom tubing evolves to meet and exceed expectations. Technical improvements and a booming customization market enable users in virtually every sector to implement futureproof, standards-compliant solutions. Whether upgrading mission-critical infrastructure, designing new communications backbones, or protecting the most sensitive wiring in harsh settings, the right split loom tubing—chosen for its size, material, manufacturer, and tailored specifications—continues to set the standard for safe, reliable, and orderly cable management.
Through continued innovation and proven field results, 2 inch split loom tubing is likely to remain a foundational element in modern wiring protection for years to come.
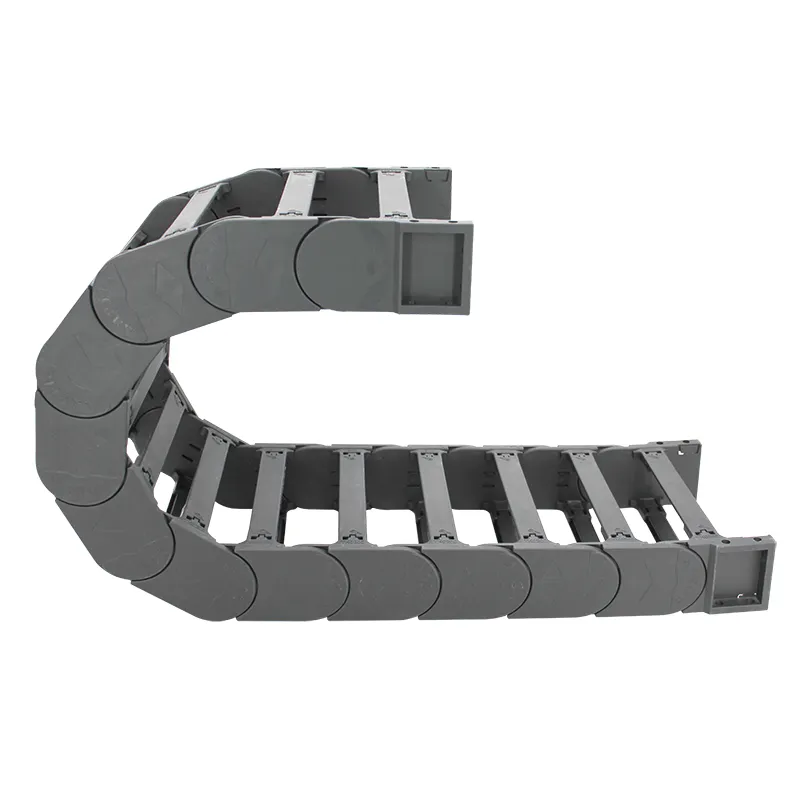
(2 inch split loom tubing)