1% 202% Wire Loom for Organizing Cables Efficiently in Your Home or Office
Understanding the Importance of 1% 202% Wire Loom
In the world of manufacturing and industrial applications, the proper organization and protection of wires are crucial for ensuring safety, reliability, and efficiency. One product that plays a significant role in this domain is the wire loom. Among various specifications and standards, the term 1% 202% wire loom has garnered attention for its unique properties and applications. This article will explore what wire looms are, the significance of the 1% 202% specification, and their implications in various industries.
What is Wire Loom?
Wire looms, also known as wire conduits or wire sleeves, are used to bundle, protect, and organize multiple wiring harnesses. They are typically made from durable materials such as plastic or flexible metal, designed to withstand harsh environmental conditions. Wire looms serve multiple purposes preventing abrasion, reducing electromagnetic interference, and simplifying assembly processes. This organization not only minimizes the risk of damage but also improves the overall aesthetics of the installation.
The Significance of 1% 202% Specification
The 1% 202% designation refers to specific performance attributes of a wire loom. Although these figures may sound cryptic, they represent the material properties that enhance the wire loom's efficiency in various applications.
1. 1% Specification The 1% component likely refers to a tolerance level or a specific performance metric. This could denote the maximum allowable expansion, contraction, or flexibility under stress. In the field of manufacturing, a tolerance of 1% is often crucial to ensure the loom fits perfectly in assemblies where precision is paramount. Misalignment or fitting issues can lead to operational failures or safety hazards, making such specifications vital.
2. 202% Specification The 202% specification is somewhat less common and could indicate a measure related to the wire loom's durability or resilience under certain conditions, such as temperature extremes or chemical exposure. If interpreted as an indicator of tensile strength or flexibility, it suggests that the wire loom can endure significant wear and tear, making it an excellent choice for challenging environments.
1 2 wire loom
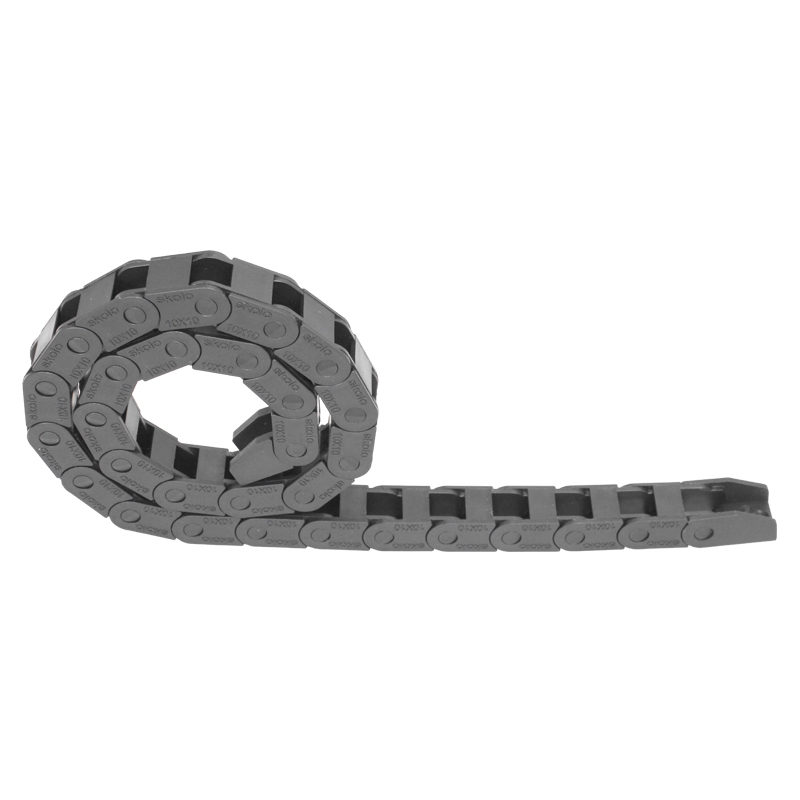
Applications of 1% 202% Wire Loom
Wire looms that meet the 1% 202% criteria are exceptionally versatile and find applications across various industries
- Automotive Industry In automobiles, wire looms are essential for organizing electronic wiring. As vehicles become increasingly reliant on sophisticated electrical systems, the need for reliable wire management solutions grows. Wire looms protect wiring from heat, moisture, and movement, ensuring optimal performance and longevity.
- Aerospace Sector In aviation, where safety and reliability are paramount, the use of high-quality wire looms is critical. The 1% 202% specification ensures that wire looms can withstand the extreme conditions and loads encountered in flight.
- Industrial Manufacturing Machinery involves a complex array of electrical systems. The right wire loom not only protects wires from mechanical abrasion but also helps prevent electrical faults. The durability indicated by the 202% metric means that these looms can function effectively in rugged industrial environments.
- Consumer Electronics Even in everyday products, wire looms help maintain a clean, orderly appearance while protecting delicate wiring from damage. Products ranging from smartphones to home appliances benefit from high-quality wire management.
Conclusion
The significance of 1% 202% wire loom cannot be understated. As industries evolve and the demand for more complex electronic systems increases, the need for reliable harnessing solutions becomes all the more prominent. Understanding the specifications and applications of wire looms is essential for engineers and manufacturers alike, ensuring safety and efficiency in every wiring system. Looking ahead, we can anticipate ongoing advancements in wire loom technology, further enhancing their protective capabilities and compliance with rigorous industry standards.